Iron ore mining is a multi-step process that involves various methods depending on the location, depth, and quality of the ore. Here's a general overview of how it's done:
-
Exploration and Planning:
- Geological Surveys: Geologists conduct surveys and use methods such as drilling and sampling to determine the presence and volume of iron ore.
- Feasibility Studies: Economic analyses and environmental assessments are performed to determine if mining the ore is viable.
-
Mining Methods:
- Open-pit Mining: For ores located near the surface, large pits or quarries are dug. This method involves removing layers of soil and rock, called overburden, to reach the ore.
- Underground Mining: For deeper ore deposits, tunnels or shafts are dug to reach the ore body. This method requires more engineering and safety considerations.
-
Extraction:
- Blasting: Explosives are used to break up the rock into manageable pieces.
- Hauling: Heavy machinery such as trucks, shovels, and conveyor belts transport the broken ore to processing plants.
-
Processing:
- Crushing and Grinding: The ore is crushed and ground to liberate the iron from other minerals.
- Concentration: Methods like magnetic separation or flotation concentrate the iron content by removing impurities.
-
Pelletizing or Sintering:
- The fine iron ore particles are agglomerated into pellets or sinters, which are easier to handle and smelt.
-
Smelting and Refining:
- The concentrated ore is then transformed into usable metal through smelting, which typically involves heating the ore alongside a reducing agent like coke in a blast furnace to produce molten iron.
-
Transport:
- The final product is transported to steel mills or customers using various modes such as rail, ship, or truck.
-
Environmental Management:
- Throughout the process, companies must adhere to environmental regulations, including managing waste, mitigating dust and noise, and rehabilitating mining sites.
This sequence ensures that iron ore is efficiently and sustainably extracted to meet global demands.
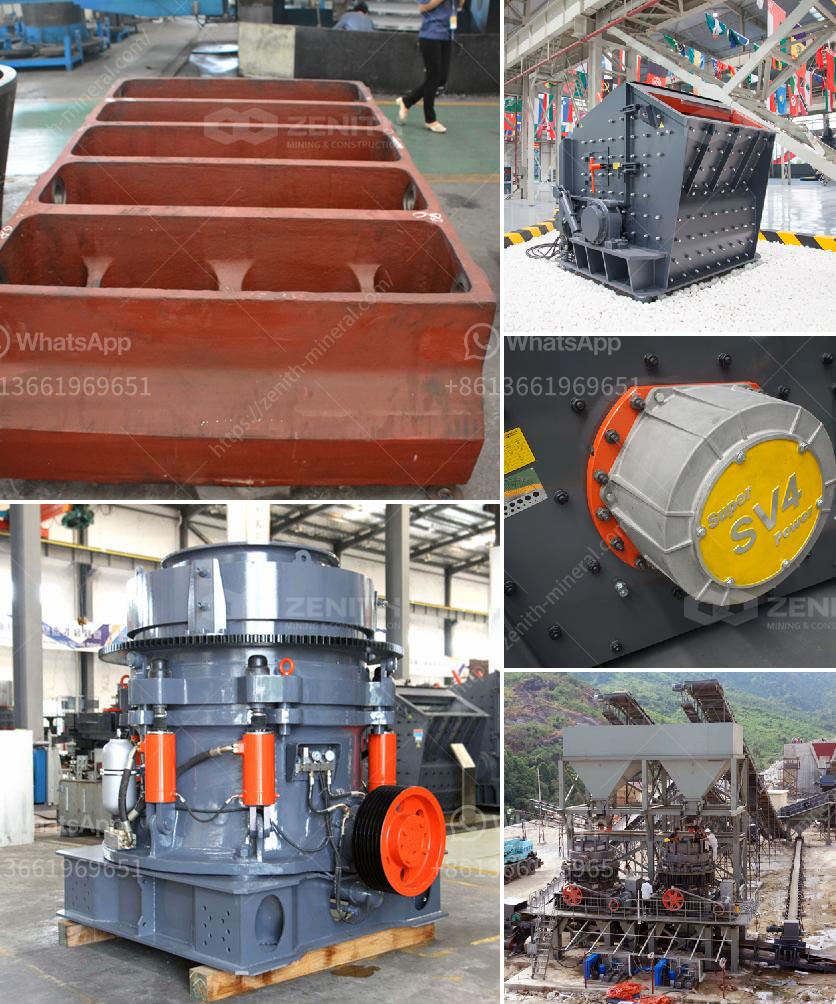