Increasing the productivity of a cone crusher involves several strategies and considerations. Here are some detailed steps and tips to help you achieve this:
1. Regular Maintenance and Inspection
Regular maintenance is crucial for the efficient operation of a cone crusher. This includes:
- Lubrication: Ensure that the crusher is properly lubricated. Regularly check the oil levels and quality. Contaminated or low oil can lead to increased wear and tear.
- Wear Parts: Inspect wear parts such as the mantle and concave. Replace them when they are worn out to maintain optimal crushing efficiency.
- Tightening Bolts: Regularly check and tighten all bolts and fasteners to prevent any loose parts that could cause damage or inefficiency.
2. Optimize Feed Size and Distribution
The feed size and distribution can significantly impact the productivity of a cone crusher:
- Uniform Feed: Ensure that the feed is distributed evenly around the crushing chamber. Uneven feed can lead to uneven wear and reduced efficiency.
- Correct Feed Size: The feed size should be appropriate for the crusher. Too large feed can cause blockages, while too small feed can reduce the crushing efficiency.
3. Adjust the Crusher Settings
Adjusting the settings of the cone crusher can help optimize its performance:
- Closed Side Setting (CSS): Adjust the CSS to ensure that the crusher is operating at its optimal setting. A smaller CSS can increase the product size, while a larger CSS can increase the throughput.
- Speed and Stroke: Adjust the speed and stroke of the crusher to match the material being processed. This can help improve the crushing efficiency and product quality.
4. Monitor and Control the Crusher Operation
Using advanced monitoring and control systems can help improve the productivity of a cone crusher:
- Automation Systems: Implement automation systems that can monitor the crusher’s performance and make real-time adjustments to optimize its operation.
- Sensors and Alarms: Use sensors and alarms to detect any issues such as blockages, low oil levels, or high temperatures. This can help prevent downtime and maintain productivity.
5. Improve the Crushing Process
Optimizing the overall crushing process can also help increase the productivity of a cone crusher:
- Pre-screening: Use pre-screening to remove fines and smaller particles before they enter the crusher. This can help reduce the load on the crusher and improve its efficiency.
- Crushing Stages: Use multiple crushing stages to achieve the desired product size. This can help improve the overall efficiency and productivity of the crushing process.
6. Training and Skill Development
Ensure that the operators are well-trained and skilled in operating the cone crusher:
- Operator Training: Provide regular training to the operators on the best practices for operating and maintaining the cone crusher.
- Skill Development: Encourage skill development and knowledge sharing among the operators to improve their understanding of the crusher’s operation and maintenance.
7. Use High-Quality Materials and Components
Using high-quality materials and components can help improve the durability and efficiency of the cone crusher:
- Wear-Resistant Materials: Use wear-resistant materials for the wear parts to extend their lifespan and reduce the frequency of replacements.
- Quality Components: Ensure that all components used in the crusher are of high quality and meet the required specifications.
By following these detailed steps and tips, you can significantly increase the productivity of your cone crusher, ensuring efficient and reliable operation.
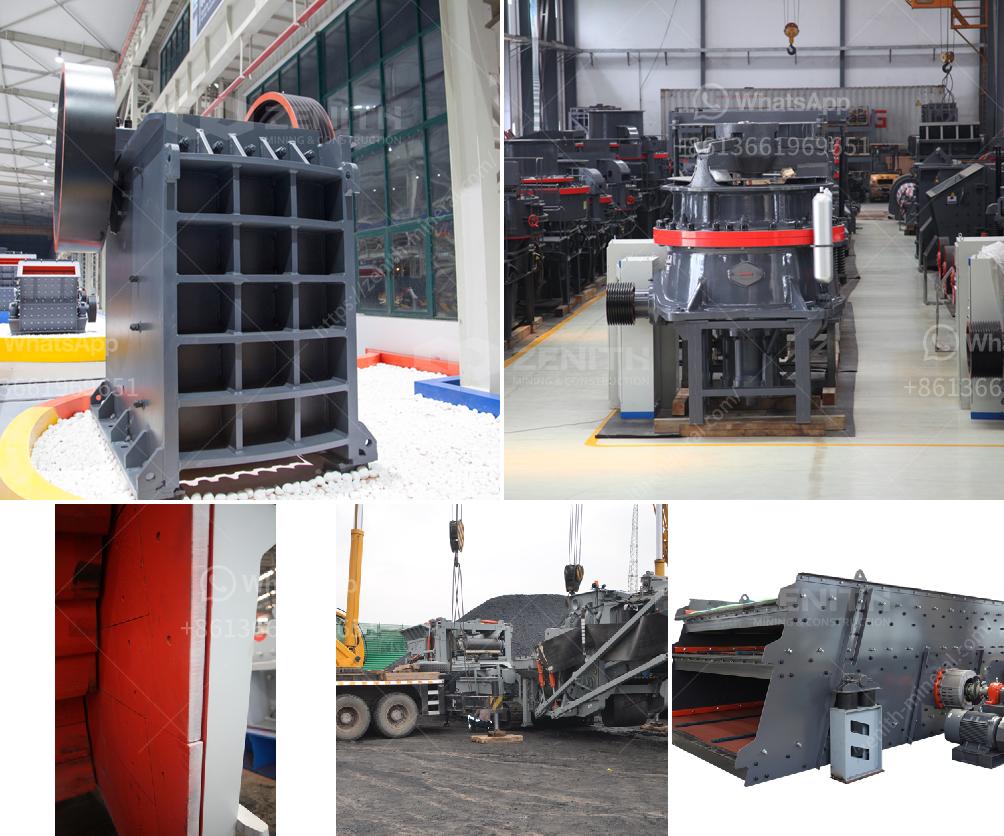