Calculating crusher production costs involves several variables and steps to ensure accuracy. Here's a basic outline to follow:
-
Material Costs:
- Raw material cost: Determine the cost of the raw material per unit volume (e.g., per ton).
- Transportation costs: Include the cost of transporting raw materials to the crusher site.
-
Operating Costs:
- Energy consumption: Calculate the cost of fuel or electricity used by the crusher.
- Labor costs: Account for the wages of employees operating the crusher and associated machinery.
- Maintenance and repairs: Include regular maintenance expenses and costs for unforeseen repairs.
-
Depreciation:
- Equipment depreciation: Factor in the depreciation of the crusher and other associated machinery over its useful life. This can be done using straight-line depreciation or more advanced methods.
-
Overheads:
- General overheads: Include indirect costs like administrative expenses, facility rent, and utilities.
-
Production Volume:
- Output volume: Determine the volume of material processed over a certain period, typically measured in tons.
- Yield efficiency: Assess the efficiency and yield of the crushing process to adjust for any material losses or inefficiencies.
Once you have all these variables, you can use the following formula to calculate the unit production cost:
\[ \text{Production Cost Per Unit} = \frac{\text{Total Costs}}{\text{Total Units Produced}} \]
Where:
- Total Costs is the sum of Material Costs, Operating Costs, Depreciation, and Overheads.
- Total Units Produced is the total volume of material processed.
For example, if your total costs amount to $50,000 and you processed 1,000 tons of material, the production cost per ton would be:
\[ \text{Production Cost Per Ton} = \frac{50,000}{1,000} = $50 \text{ per ton} \]
Keep in mind that these are general guidelines, and actual calculations might require more detailed and specific data based on your situation. Adjust the variables as necessary to fit your particular cost structure and operational details.
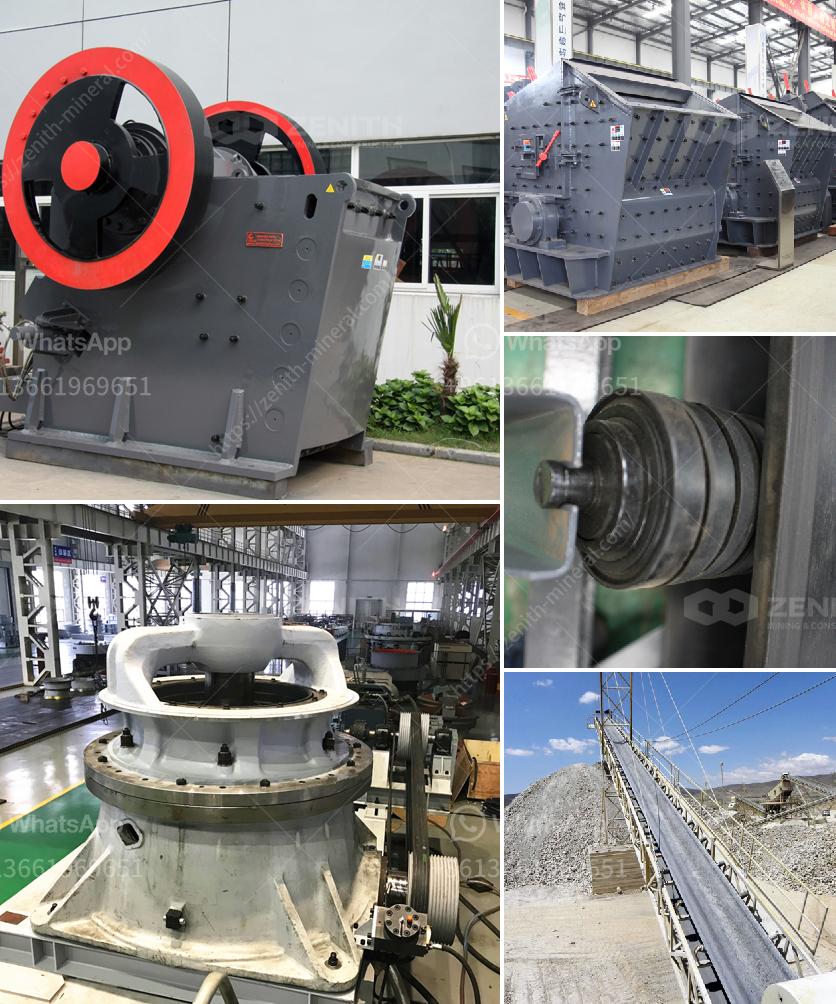