Designing a 15 tons per hour (tph) barite recovery process plant entails several essential steps and considerations. Here’s a high-level overview of what such a plant might look like:
Process Flow
-
Crushing and Screening:
- Raw barite ore is initially crushed using a jaw crusher or cone crusher.
- The crushed material is then screened to separate fine particles.
-
Grinding:
- The screened material is sent to a grinding mill to achieve the desired particle size.
- Grinding is typically done using ball mills, rod mills, or similar equipment.
-
Gravity Separation:
- The ground material is then passed through gravity separation units such as jigs, spirals, or shaking tables to concentrate the high-density barite from the low-density waste.
-
Flotation (Optional):
- If higher purity is required, flotation can be employed to further concentrate the barite by removing impurities.
- Reagents and conditioning tanks are involved in this step.
-
Thickening and Dewatering:
- The slurry from the separation process is thickened and dewatered using thickeners and filters.
- This results in a barite concentrate with reduced moisture content.
-
Drying (Optional):
- If the end-use requires dry barite, the product is dried using rotary dryers or fluidized bed dryers.
-
Packaging and Storage:
- The final concentrated and dried barite is then stored and packaged for transport.
Key Equipment
- Primary Crusher (e.g., Jaw Crusher)
- Secondary Crusher (e.g., Cone Crusher)
- Grinding Mill (e.g., Ball Mill or Rod Mill)
- Gravity Separation Equipment (e.g., Jigs, Shaking Tables)
- Flotation Cells (if needed)
- Thickener
- Filter Press
- Dryer (if needed)
- Conveyors and Feeders for material handling
Considerations
By carefully considering these components, a 15 tph barite recovery process plant can be designed to efficiently and economically process barite ore while maximizing recovery and meeting industry standards.
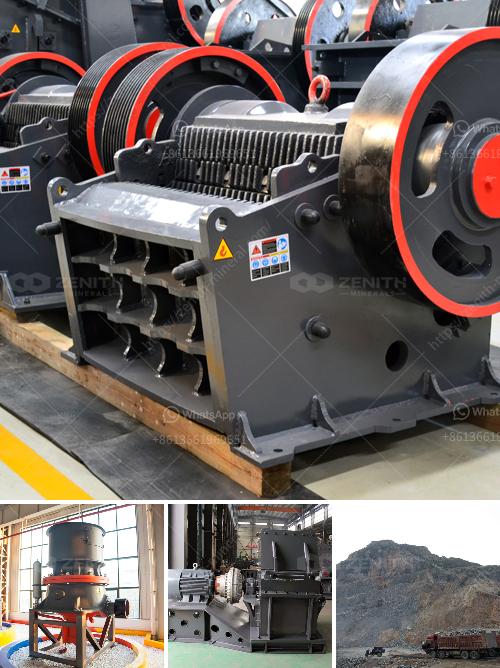