Designing a hopper feeder involves several steps to ensure efficient and reliable material handling. Here’s a guide to help you through the process:
1. Define the Requirements
- Material Characteristics: Understand the physical properties of the material to be fed (e.g., particle size, bulk density, moisture content).
- Flow Rate: Determine the required feed rate to match the process needs.
- Environmental Conditions: Consider the operating environment, including temperature, humidity, and potential for corrosion or wear.
2. Choose the Hopper Shape
- Cone Hoppers: Suitable for free-flowing materials.
- Wedge Hoppers: Better for materials prone to bridging (where the material forms a bridge and stops flowing).
- Transition Hoppers: Combine attributes of conical and wedge designs for complex applications.
3. Select the Hopper Volume
- Holding Capacity: Ensure the hopper holds a sufficient amount of material to minimize the frequency of refilling.
- Material Reserve: Consider a buffer volume to prevent process interruptions.
4. Flow Assistance Devices
- Vibrators: Help in preventing bridging and ensuring steady material flow.
- Aerators: Useful for fine or cohesive powders.
- Mass Flow or Funnel Flow: Decide whether mass flow (where all material moves concurrently) or funnel flow (central core moves) is ideal depending on material properties.
5. Feeder Selection
- Gravimetric Feeders: Measure and control the mass flow rate, suitable for precision applications.
- Volumetric Feeders: Control the volume flow rate, suitable for less critical applications.
- Belt Feeders: Good for large, bulky materials.
- Screw Feeders: Versatile and can handle various materials including powders and granules.
- Vibratory Feeders: Suitable for small and medium-sized particles.
6. Design Mechanics
- Discharge Opening: Size the opening to ensure a consistent flow rate without clogging.
- Incline Angle: Design the hopper walls at an angle steep enough to prevent material from sticking, typically above the angle of repose of the material.
- Material Flow Analysis: Use software to model and predict material behavior within the hopper.
7. Safety and Maintenance
- Access Points: Design access for routine maintenance and inspection.
- Safety Gates/Valves: Integrate shut-off mechanisms to block material flow during maintenance or emergencies.
- Wear Protection: Use liners or coatings in high-wear areas to prolong the life of the hopper feeder.
8. Integration with Control Systems
- Sensors: Install sensors to monitor hopper levels and flow rates.
- Control Units: Use programmable logic controllers (PLCs) to automate and optimize feeding processes.
9. Prototyping and Testing
- Prototype Development: Build a small-scale model to test the design under real-world conditions.
- Performance Assessment: Evaluate the prototype for feed rate accuracy, consistency, and material handling issues.
10. Final Design Adjustments
- Iterate: Refine the design based on prototype testing results.
- Optimize: Make necessary adjustments to the dimensions, angles, and components to achieve the desired performance.
By following these steps, you can design a hopper feeder tailored to your specific material handling needs while ensuring efficiency, reliability, and safety.
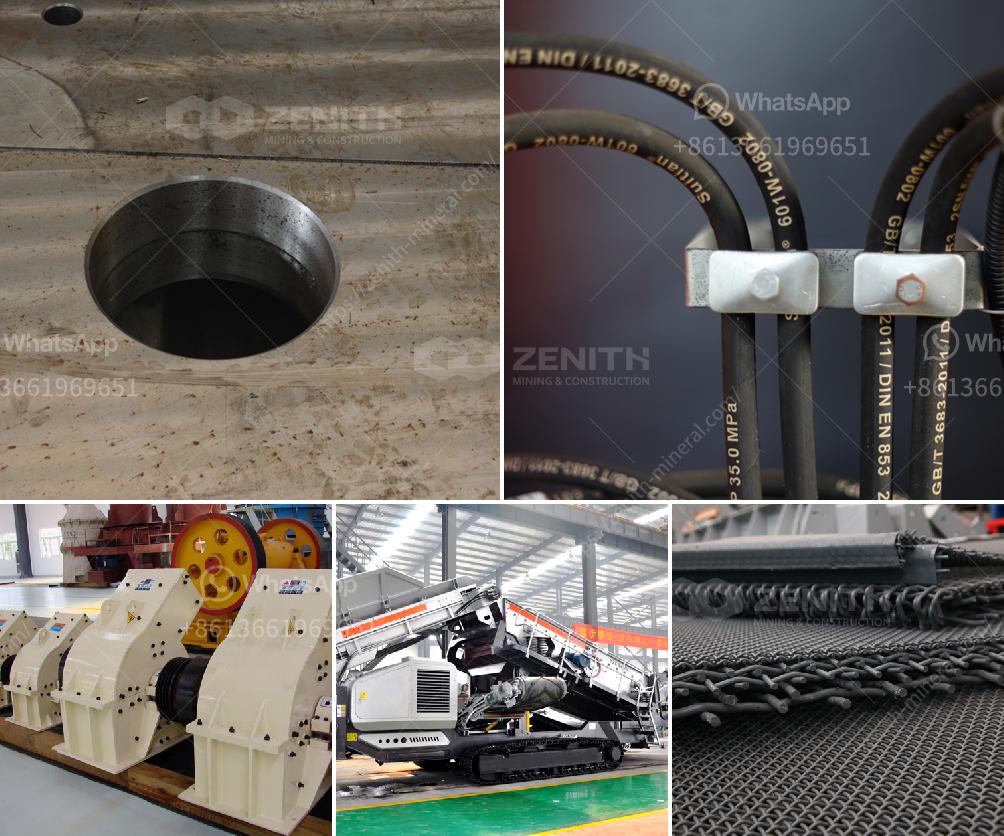