Certainly! Here's a streamlined 75 tons per hour (tph) limestone crushing process:
Step 1: Primary Crushing
- Equipment: Jaw Crusher
- Input Size: ≤700 mm
- Output Size: 100-200 mm
- Description: The raw limestone is fed into the jaw crusher where it is crushed to a manageable size for the next stage.
Step 2: Secondary Crushing
- Equipment: Impact Crusher or Cone Crusher
- Input Size: ≤200 mm
- Output Size: 20-50 mm
- Description: The material from the jaw crusher is further reduced in size in the impact or cone crusher.
Step 3: Screening
- Equipment: Vibrating Screen
- Decks: Usually 2 or 3-deck screens are used.
- Output Size: Various sizes (typically 0-5 mm, 5-20 mm, and 20-50 mm)
- Description: The crushed material is separated into different size fractions. The correctly sized materials are sent to the final product pile, while oversized materials may be returned for further crushing.
Step 4: Material Handling
- Equipment: Conveyor Belts
- Description: Conveyor belts transfer material between different stages of the crushing process and to the final stockpiles or further processing stages.
Add-Ons (Optional)
- Dust Suppression: Various methods like water sprays or dust collection systems to minimize dust.
- Automation and Control Systems: To optimize the process and monitor the performance of machines in real-time.
Output
- Final Product: Limestone aggregates of different sizes suitable for various construction and industrial applications.
Given that actual equipment choice may vary based on specific project requirements, material characteristics, and site conditions, this is a general overview. For a more customized solution, consulting with equipment manufacturers or specialists is recommended.
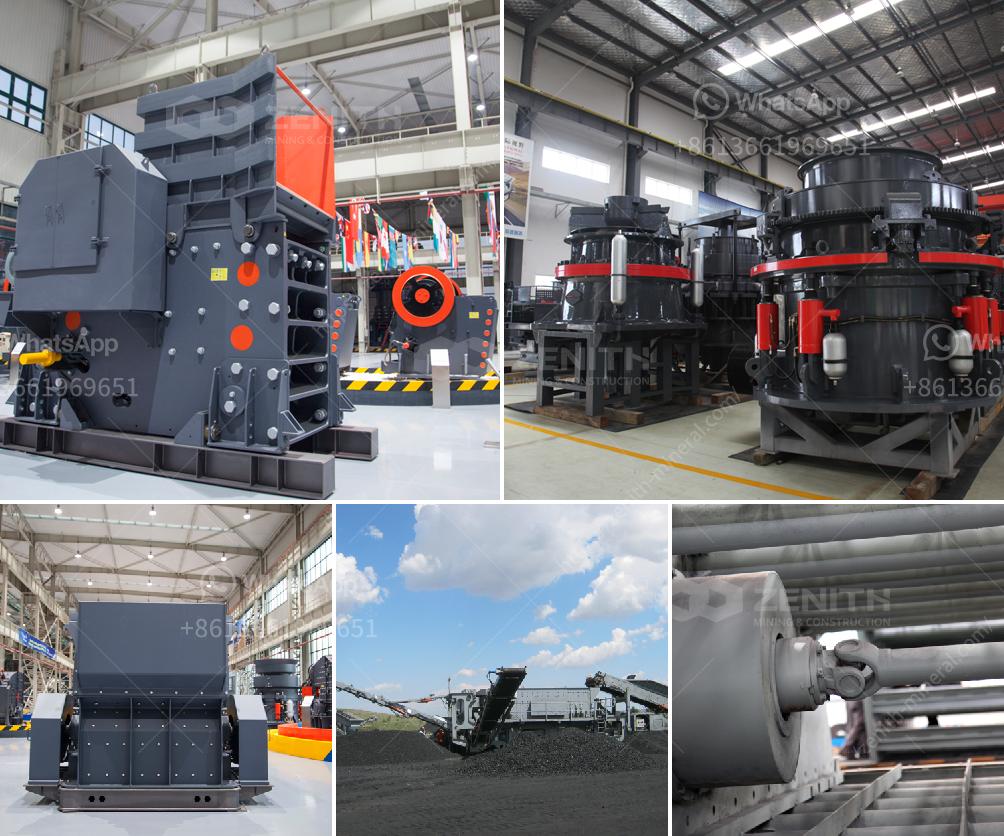