Calculating the running cost of a crusher involves several steps and considers multiple factors. Here’s a simplified process to get you started:
1. Initial Cost and Depreciation
- Purchase Price: The upfront cost of purchasing the crusher.
- Depreciation: Spread the purchase price over the projected lifespan of the crusher to determine the annual depreciation cost.
2. Operating Costs
- Fuel/Energy Consumption:
- Calculate the amount of fuel or electricity required to run the crusher.
- Multiply by the cost per unit of fuel or electricity.
- Maintenance and Spare Parts:
- Include regular maintenance (lubrication, inspections, replacements) and unplanned repairs.
- Keep a record of historical data for accurate estimates.
- Labor Costs:
- The cost associated with operators and maintenance personnel.
3. Consumables
- Wear Parts: Consider the frequency and cost of replacing wear parts (e.g., jaw plates, cone liners, blow bars).
- Lubricants and Hydraulic Fluids: Regular replacement and associated costs.
4. Other Costs
- Insurance and Taxes: Include annual insurance and any applicable taxes.
- Transportation: Periodic costs for moving the crusher if it is mobile.
5. Total Running Cost Calculation
Add up all the components listed above to determine the total running cost:
6. Cost per Metric Ton
To get a per-ton cost, divide the total running cost by the amount of material processed:
Example Calculation:
-
Initial Cost and Depreciation:
- Purchase Price: $200,000
- Lifespan: 5 years
- Annual Depreciation: $200,000 / 5 = $40,000
-
Operating Costs (Annual):
- Fuel: $30,000
- Maintenance: $15,000
- Labor: $50,000
-
Consumables:
- Wear Parts: $25,000
- Lubricants: $5,000
-
Other Costs:
- Insurance: $10,000
- Transportation: $5,000
-
Total Running Cost:
- Total: $40,000 (Depreciation) + $30,000 (Fuel) + $15,000 (Maintenance) + $50,000 (Labor) + $25,000 (Wear Parts) + $5,000 (Lubricants) + $10,000 (Insurance) + $5,000 (Transportation) = $180,000
-
Cost per Metric Ton:
- Total Material Processed: 100,000 tons annually
- Cost per Ton: $180,000 / 100,000 = $1.80 per ton
Conclusion
Regularly update and refine these figures with actual data to ensure accuracy. Keep in mind that these costs can vary based on factors such as local fuel prices, labor rates, and the nature of the material being processed.
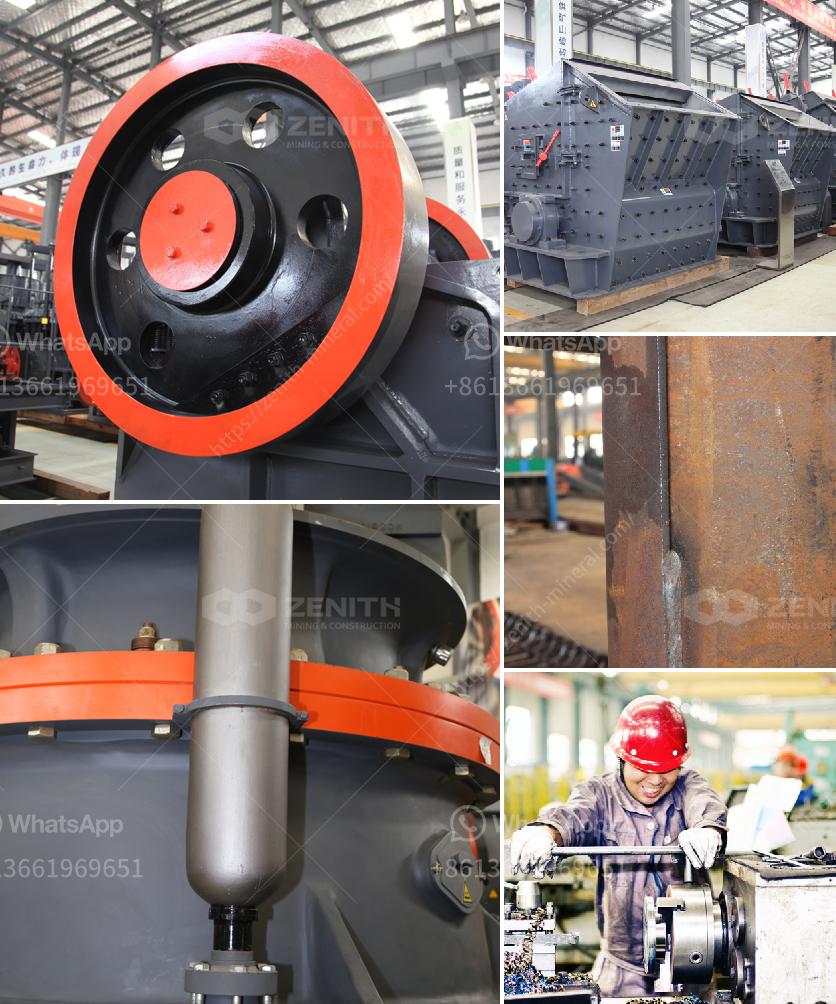