The difference between a single-toggle and double-toggle crusher lies primarily in the mechanism that moves the jaw, which impacts performance and use-case suitability. Here's a breakdown:
-
Single-Toggle Crusher:
- Mechanism: Uses a single toggle plate.
- Motion: The swing jaw is suspended on the eccentric shaft, which causes a compressive action. The toggle plate directly links with the swing jaw, causing it to move up and down as the pitman (moving part) and eccentric rotate.
- Efficiency: Generally more efficient with a higher throughput rate, making it suitable for larger production operations.
- Maintenance: Fewer parts and simplicity in design often result in lower maintenance requirements.
- Weight and Cost: Typically lighter and less expensive than double-toggle crushers.
-
Double-Toggle Crusher:
- Mechanism: Utilizes two toggle plates.
- Motion: The swing jaw is pivoted with two bearings on the frame. This leads to a purely compressive action movement without rubbing, from the top of the swing mechanism (producing a more uniform output size). It keeps the jaw movement more consistent and generates less abrasive action.
- Crushing Strength: Generally provides a more robust crushing action and can produce a more precise and uniform product size. Useful for harder materials.
- Maintenance: More parts and a complex design can lead to higher maintenance demands.
- Weight and Cost: Heavier and typically more expensive due to the increased complexity.
In summary, single-toggle crushers are often favored for their efficiency, lower cost, and simpler maintenance, while double-toggle crushers are preferred for their robust crushing action, particularly with harder materials.
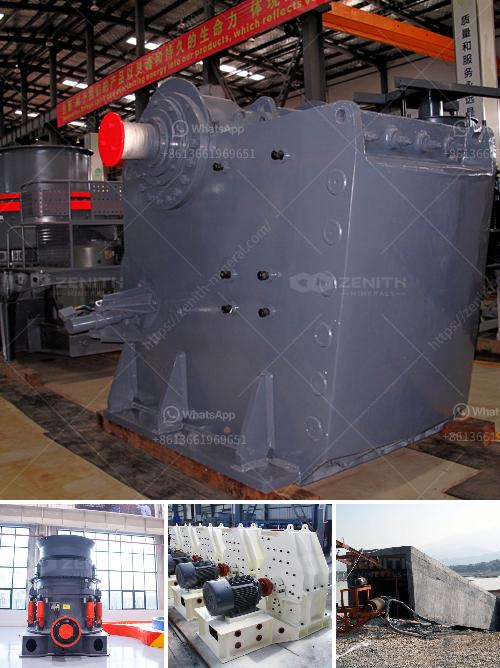