Starting a mini cement mill is a complex endeavor that involves various technical, financial, and regulatory considerations. Here's a step-by-step guide to help you get started:
1. Conduct Market Research
- Assess demand: Understand the market demand for cement in your region.
- Identify competitors: Analyze the competition to find a viable market position.
2. Create a Business Plan
- Define scope: Outline the scale and capacity of your mill.
- Financial projections: Include estimated costs and potential revenues.
- Funding strategy: Determine how you will finance the project (loans, investors, personal funds).
3. Obtain Necessary Permits and Licenses
- Environmental clearance: Cement production can impact the environment, so you'll need clearance from relevant authorities.
- Business registration: Register your business and obtain any industry-specific licenses.
4. Site Selection
- Location: Choose a location that is accessible to raw materials (limestone, clay, etc.) and close to your target market.
- Infrastructure: Ensure the site has adequate infrastructure, such as electricity, water, and transportation links.
5. Procurement of Machinery and Equipment
- Core machinery: Purchase essential equipment like crushers, rotary kilns, ball mills, and conveyors.
- Supporting equipment: Buy supplementary items such as storage silos, packing machines, and dust collectors.
6. Raw Material Sourcing
- Suppliers: Identify reliable suppliers for raw materials like limestone, clay, and gypsum.
- Contracts: Secure long-term contracts to ensure a consistent supply.
7. Infrastructure Setup
- Civil construction: Build the necessary infrastructure including factory buildings and administrative offices.
- Machinery installation: Install the core machinery and set up auxiliary equipment.
8. Hiring and Training Staff
- Skilled labor: Hire experienced technical staff to operate the machinery.
- Training programs: Conduct training sessions for staff to ensure efficient and safe operations.
9. Implement Quality Control Measures
- Lab setup: Set up a lab for quality testing of raw materials and finished products.
- Standards compliance: Ensure your production meets industry quality standards.
10. Production Planning and Trial Runs
- Initial production plan: Develop a detailed production schedule.
- Trial runs: Conduct trial production runs to fine-tune the process and address any technical issues.
11. Marketing and Distribution
- Marketing strategy: Develop a marketing plan to promote your cement.
- Distribution network: Establish relationships with distributors and retailers.
12. Continuous Improvement
- Feedback loop: Implement a system to collect feedback from customers and distributors.
- Process optimization: Continuously optimize production processes to improve quality and reduce costs.
Key Considerations
- Environmental impact: Be compliant with environmental regulations and invest in pollution control technologies.
- Financial management: Keep a close watch on your finances to ensure profitability.
- Safety: Prioritize the safety of workers and ensure compliance with health and safety regulations.
Starting a mini cement mill is a significant investment but can be a profitable venture if managed well. Good luck!
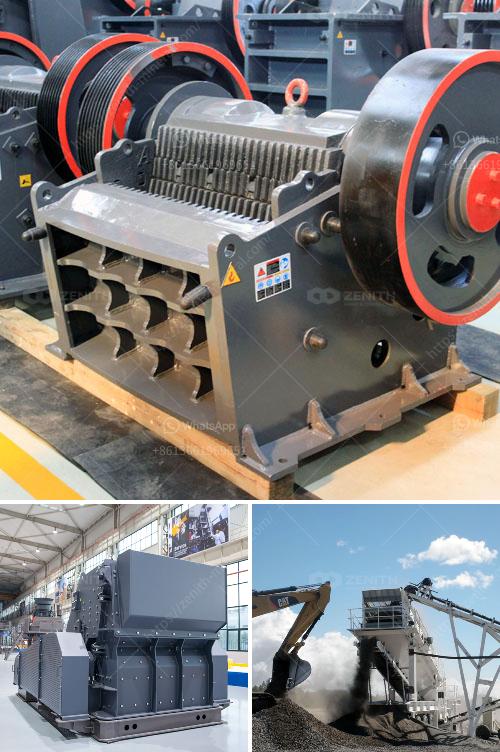