A receiving feeder in a crusher is a crucial component in the mining and aggregate industries, where it plays a significant role in the initial stages of material processing. The primary function of a receiving feeder is to regulate the flow of raw materials into the crusher, ensuring a consistent and controlled feed rate. This helps in optimizing the crusher's performance and efficiency, preventing potential issues such as overloading or uneven material distribution.
Detailed Explanation:
-
Functionality:
- Regulation of Material Flow: The receiving feeder controls the amount of material that enters the crusher. By doing so, it ensures that the crusher operates at an optimal capacity, avoiding situations where the crusher might be overwhelmed by too much material at once.
- Consistent Feed Rate: A steady and consistent feed rate is crucial for the efficient operation of the crusher. The receiving feeder helps maintain this consistency, which in turn leads to better crushing performance and reduced wear and tear on the crusher components.
-
Types of Receiving Feeders:
- Vibrating Feeders: These are the most common type of feeders used in crushing operations. They use vibration to move materials along a conveyor belt or chute, ensuring a steady flow into the crusher.
- Apron Feeders: These are heavy-duty feeders that use a series of overlapping metal plates to convey materials. They are typically used for handling large, heavy, or abrasive materials.
- Grizzly Feeders: These feeders have a series of parallel bars or rails that allow smaller materials to pass through while larger materials are fed into the crusher. This helps in pre-screening and removing fines before the crushing process.
-
Importance in Crushing Operations:
- Prevents Overloading: By regulating the flow of materials, the receiving feeder helps prevent the crusher from being overloaded, which can lead to mechanical failures or reduced efficiency.
- Improves Crusher Efficiency: A consistent feed rate ensures that the crusher operates smoothly, leading to better crushing efficiency and higher throughput.
- Reduces Wear and Tear: By preventing sudden surges of material, the receiving feeder helps reduce the wear and tear on the crusher components, extending their lifespan and reducing maintenance costs.
-
Integration with Other Equipment:
- Conveyors: Receiving feeders are often integrated with conveyor systems that transport materials from one stage of the processing plant to another.
- Screens: In some setups, receiving feeders are combined with screening equipment to remove fines and smaller particles before the material enters the crusher.
-
Operational Considerations:
- Material Characteristics: The type of material being processed (e.g., size, hardness, moisture content) can influence the choice of receiving feeder and its settings.
- Feed Rate Adjustments: Operators may need to adjust the feed rate based on the crusher's capacity and the desired output size.
In summary, the receiving feeder is an essential component in the crushing process, ensuring that raw materials are fed into the crusher in a controlled and consistent manner. This not only optimizes the crusher's performance but also helps in maintaining the overall efficiency and longevity of the crushing operation.
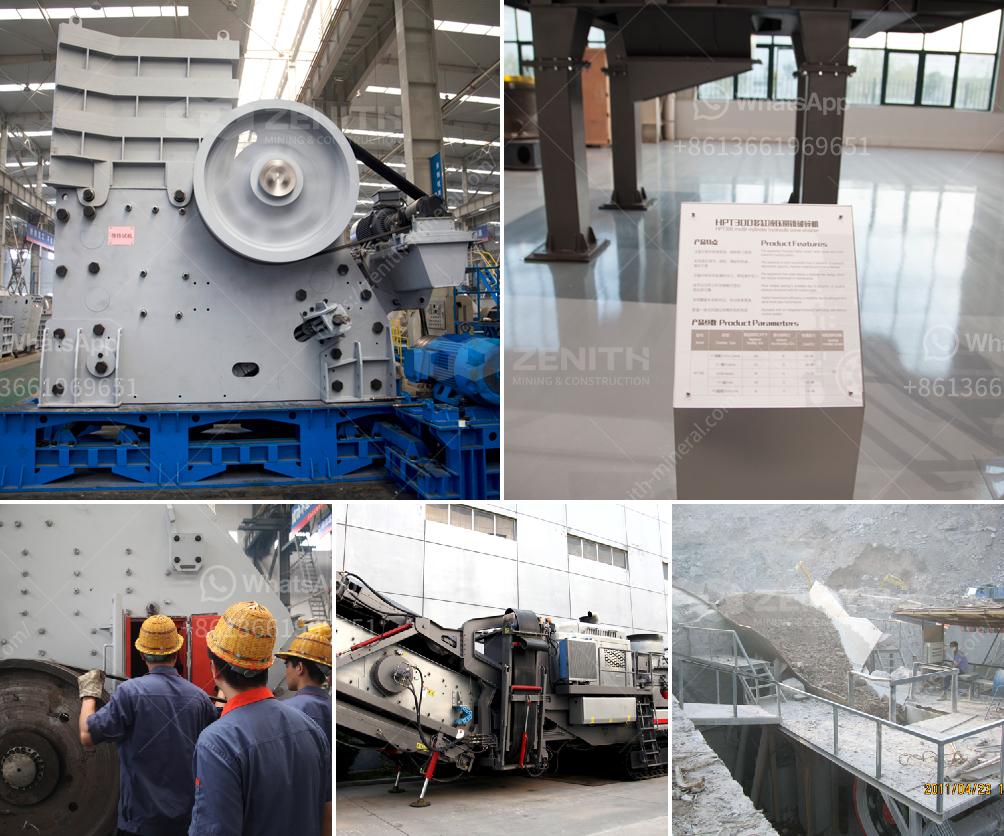