Impact crushers and jaw crushers are both commonly used in the aggregate and mining industries, but they perform different roles and have distinct characteristics:
-
Crushing Principle:
- Jaw Crusher: Utilizes compressive force to crush materials. It has two jaws, one fixed and one movable, which move in a V-shaped motion to break down materials.
- Impact Crusher: Uses impact force to crush materials. It has a high-speed rotor with blow bars that throw the material against stationary anvils or curtains to achieve reduction.
-
Material Suitability:
- Jaw Crusher: Ideal for primary crushing of large, hard, and abrasive materials like granite, ores, and recycled concrete.
- Impact Crusher: Suitable for softer, less abrasive materials and works well for secondary and tertiary crushing. It is often used for limestone, concrete, and asphalt.
-
Output Shape:
- Jaw Crusher: Produces irregular, more angular particles.
- Impact Crusher: Tends to produce more uniform, cubical-shaped particles which can be desirable in certain applications like road construction.
-
Wear Parts:
- Jaw Crusher: Wear parts include jaw plates, which are made of manganese steel. They are relatively simple to replace and can be flipped to prolong their life.
- Impact Crusher: Wear parts include blow bars and impact plates, which are often made of high-chrome alloy. These parts can be more expensive and may require more frequent replacement due to the higher wear rate.
-
Capacity and Reduction Rate:
- Jaw Crusher: Typically offers lower capacity and a lower reduction ratio compared to impact crushers. It’s effective for primary crushing where material size is reduced significantly.
- Impact Crusher: Generally provides better capacity and higher reduction ratios, which makes it effective for producing fine materials and uniform particles.
-
Operating Costs:
- Jaw Crusher: Generally has lower operating costs due to lower wear and tear but can be less efficient in producing fine materials.
- Impact Crusher: Often has higher operating costs due to frequent replacement of wear parts but offers better efficiency for producing finer materials.
Understanding the specific requirements of your project, such as material type, desired output, and budget, will help determine which crusher is more suitable for your needs.
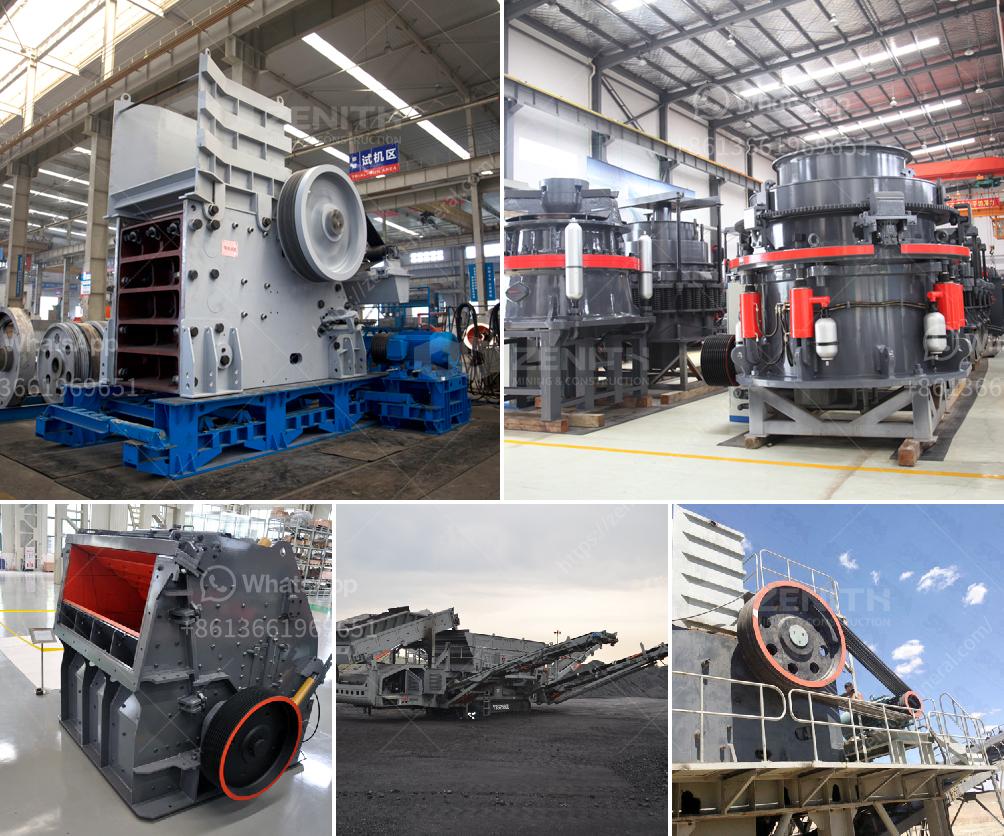