Making plaster from phosphogypsum involves several steps, primarily focusing on the treatment and conversion of phosphogypsum into a usable form of plaster. Phosphogypsum is a byproduct of the phosphate fertilizer industry and needs to be handled carefully due to its chemical content. Below is a basic outline of the process:
Materials Needed:
- Phosphogypsum
- Water
- Lime or other neutralizing agents
- Additives (optional, for improving properties like setting time and strength)
Equipment Needed:
- Protective gear (gloves, masks, goggles)
- Mixing container
- Stirring tool or mechanical mixer
- Filter or decanting apparatus
- Kiln or drying oven (if available)
Safety Precautions:
- Always wear appropriate protective gear.
- Work in a well-ventilated area or under a fume hood to avoid inhaling dust or fumes.
- Follow local regulations for handling and disposing of any waste materials.
Step-by-Step Process:
-
Preparation of Phosphogypsum:
- Ensure the phosphogypsum is dry and free from large lumps. If necessary, dry it in a kiln or drying oven.
- Sieve the phosphogypsum to remove any impurities or large particles, ensuring a fine, homogeneous powder.
-
Neutralization:
- In a mixing container, add the phosphogypsum powder.
- Gradually add a neutralizing agent like lime (calcium hydroxide) to the phosphogypsum to reduce its acidity. The typical ratio is around 5-10% of the weight of phosphogypsum, but this may vary depending on the initial acidity level.
- Add water slowly while stirring continuously to form a slurry. The consistency should be pourable but not too runny.
-
Mixing:
- Use a mechanical mixer or a stirring tool to ensure that the neutralizing agent and phosphogypsum are thoroughly combined.
- Continue mixing to ensure uniform consistency. You can also add optional additives at this stage to improve properties such as setting time, strength, or workability.
-
Setting and Filtration:
- Allow the mixture to sit and react for some time (several hours to a day) to ensure complete neutralization.
- After adequate time, filter or decant the mixture to remove any excess water and impurities. This can be done using a filter press or similar apparatus.
-
Drying:
- The filtered plaster should be dried to remove any remaining moisture. This can be done by spreading it out in a thin layer and allowing it to air dry or using a drying oven.
-
Final Preparation:
- Once completely dry, the plaster can be ground again to ensure a fine, uniform powder if needed.
- The final product is now ready for use as plaster, which can be mixed with water to form a paste for application.
Application:
- The prepared phosphogypsum plaster can be used similarly to conventional plaster. Mix with water just before application to achieve the desired consistency.
Important Notes:
- Phosphogypsum may contain trace amounts of radioactive elements and potentially harmful impurities. Ensure proper safety and environmental precautions are followed.
- The exact ratios and conditions may vary based on the specific composition of the phosphogypsum and the intended use of the plaster.
By following these steps, you can prepare a plaster from phosphogypsum that can be used for various building and construction purposes.
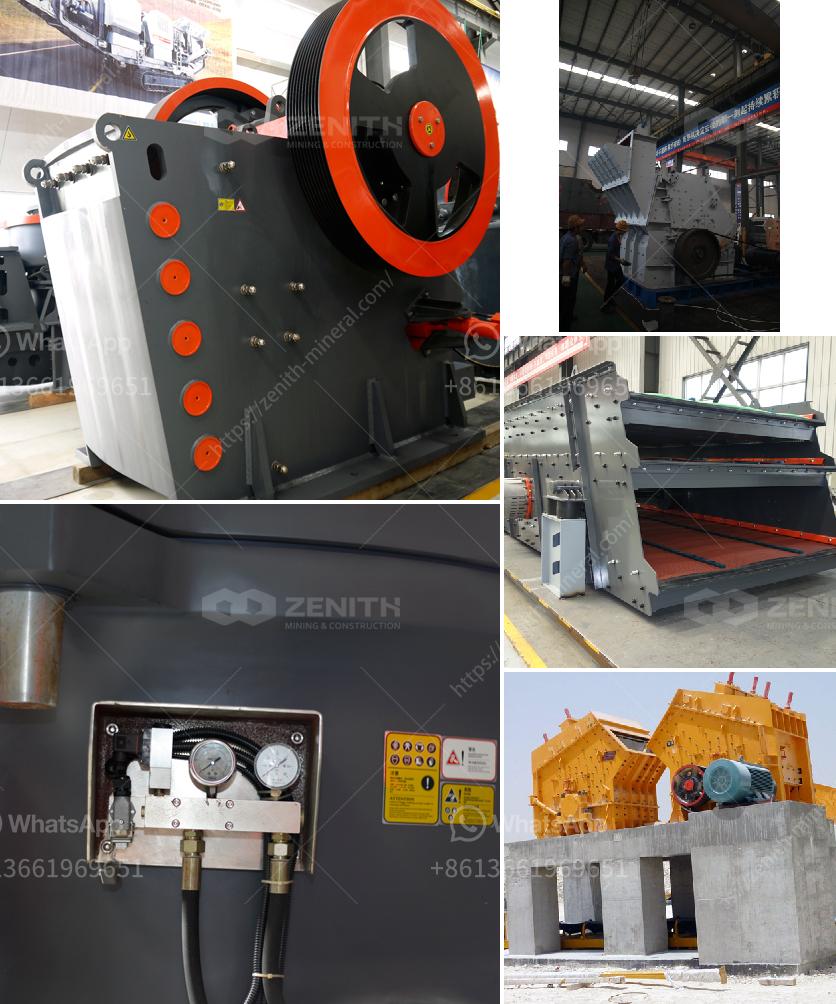