Separating iron from manganese commonly involves a series of physical and chemical processes. Here is a step-by-step method that is often used in industry:
1. Gravity Separation:
- Crushing and Grinding: First, the ore containing both iron and manganese is crushed and ground into fine particles.
- Dense Media Separation: The ground particles are then subjected to dense media separation (DMS) where a medium such as ferrosilicon is used. Because manganese has a higher density than iron, it will sink while iron ore floats, allowing for an initial physical separation.
2. Magnetic Separation:
- Magnetic Separation: Manganese is not magnetic, while iron is magnetic. Use a magnetic separator to attract the iron particles and separate them from the manganese particles.
3. Chemical Methods:
- Leaching Processes: In cases where the ores are strongly bound together, a chemical process such as hydrometallurgical leaching may be used. For instance, the use of sulfuric acid to dissolve manganese, leaving solid iron behind.
- Reduction Roasting: Another technique involves reduction roasting followed by acid leaching. The manganese oxides are reduced to manganous oxide, which then reacts with the leach solution more readily than iron oxide.
4. Electrolytic Methods:
- Electrolytic Process: Manganese can be electrolytically reduced and then separately collected, especially in refining processes where high purity manganese is needed.
Each method's applicability depends on the specific nature of the ore and the desired purity of the separated metals. In industrial applications, a combination of these processes is often used to achieve optimal separation.
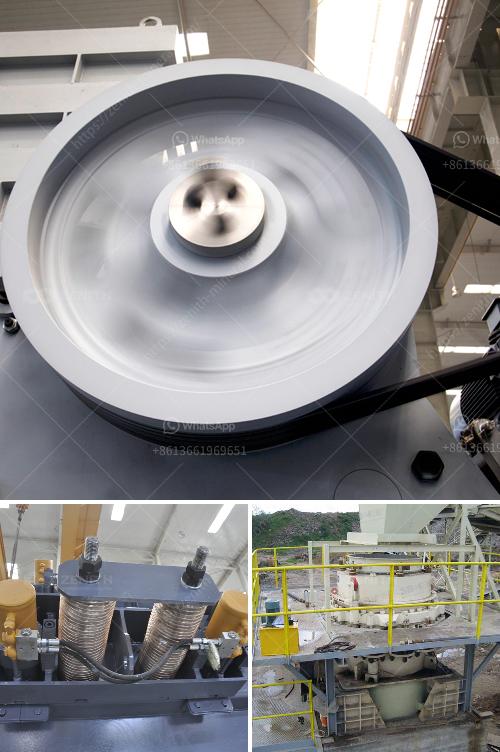