A 5 tons per hour (tph) rock chrome ore concentration plant is a facility designed to process and concentrate chrome ore, or chromite, from mined rock. Here’s a brief overview of what such a plant typically involves:
Key Components:
-
Feeding System:
- Hopper and Feeder: Used to feed the ore into the processing plant in a controlled manner.
-
Comminution (Crushing and Grinding):
- Jaw Crusher or Gyratory Crusher: Reduces large rocks to smaller sizes.
- Ball Mill or Rod Mill: Further grinds crushed ore to finer particles to liberate the chromite minerals from the rock matrix.
-
Concentration Equipment:
- Shaker Table: Utilized for gravity separation, capitalizing on density differences between chromite and other minerals.
- Spiral Chutes: Another gravity concentration method to segregate fine chromite ore particles.
- Jig Machine: Employs pulsating water to separate chromite based on its weight.
- Magnetic Separator: Removes magnetic impurities if present.
-
Thickening and Filtration:
- Thickeners: Concentrate the slurry to reduce water content.
- Filters: Extracts water from the thickened slurry to produce a dry concentrate.
-
Handling and Storage:
- Conveyor Belts: To transport the material between different stages.
- Storage Bins: For intermediate and final product storage before further processing or sale.
Process Flow:
-
Raw Material Feeding:
- Raw chrome ore is fed into the hopper and then transferred by feeders to the primary crusher.
-
Crushing and Grinding:
- The crusher breaks down the ore to smaller, manageable pieces. This is followed by milling where the ore is ground into finer particles.
-
Gravity Separation:
- Ground ore is fed to a series of gravity concentration devices like jigs, spirals, or shaking tables that exploit the differences in densities between the chromite and the gangue (unwanted minerals).
-
Magnetic Separation (if necessary):
- This step helps remove any magnetic impurities and further purifies the concentrate.
-
Thickening and Dewatering:
- The concentrated ore slurry is thickened to remove excess water. Thickeners and filter presses are typically employed.
-
Final Product Handling:
- The final chrome concentrate is dried and stored in bins before being transported or shipped out.
Considerations:
- Ore Quality and Consistency:
- Consistency in the feed grade is crucial for optimal plant performance.
- Energy Consumption:
- Energy-efficient equipment is preferred to reduce operational costs.
- Environmental Compliance:
- Ensuring the plant operates within environmental regulations to minimize ecological impact.
This plant setup aids in efficiently extracting and concentrating chrome ore from the raw rock, making it suitable for further refining processes or direct use in industrial applications.
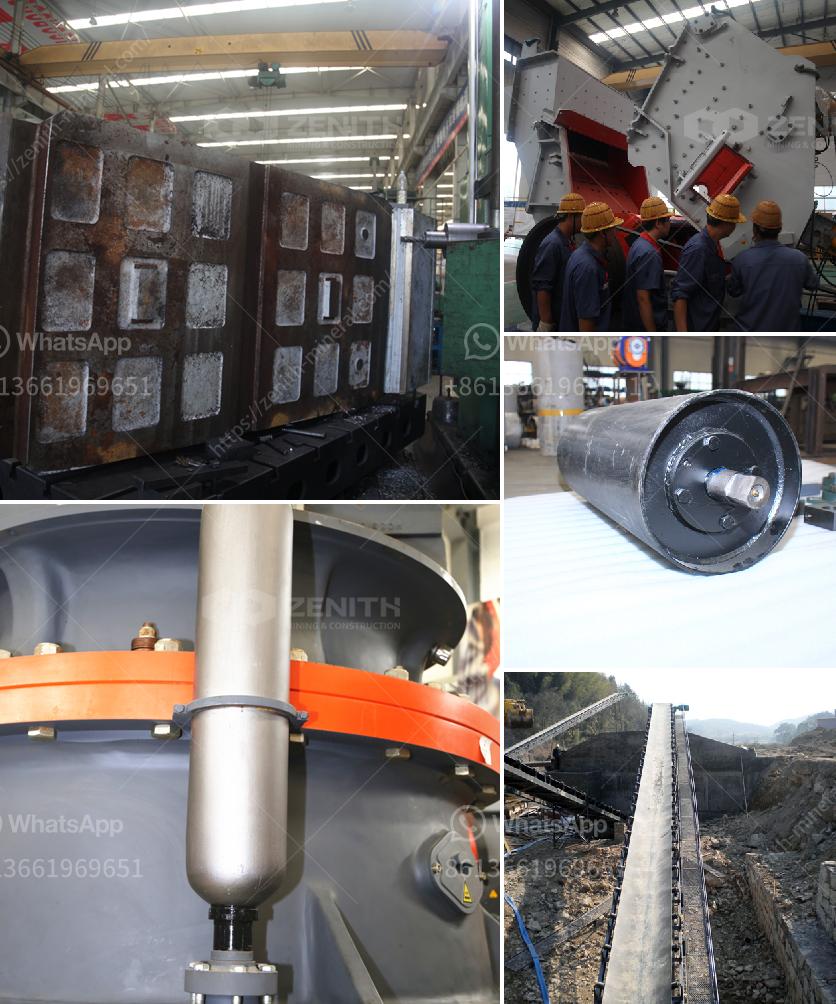