An 8 tons per hour (8tph) gold and tin extraction process typically involves several stages to ensure efficient recovery of both metals from the ore. Here’s a general overview of such a process:
-
Crushing and Grinding:
- Crushing: The ore is first crushed to reduce the size of the particles and liberate the gold and tin minerals. This is usually done in a primary jaw crusher followed by secondary and tertiary crushers.
- Grinding: The crushed material is then ground in ball mills or vertical roller mills to further reduce the particle size and free up the valuable minerals for the subsequent extraction process.
-
Classification and Concentration:
- Classification: The ground material is classified using hydrocyclones or vibrating screens to separate fine particles from coarser ones.
- Gravity Concentration: The classified material passes through gravity concentrators like jigs, spirals, or shaking tables, where the denser gold and tin particles are separated from the lighter gangue minerals based on their densities.
-
Flotation (if applicable):
- In cases where the ore contains sulfides or other impurities, flotation cells may be used to further concentrate the gold and tin by separating them from other minerals using chemical reagents and air bubbles.
-
Magnetic Separation (for Tin):
- Tin ores often contain magnetic minerals. Magnetic separation can be employed to remove these impurities. This step usually involves passing the concentrated ore through magnetic separators to pull out any iron or other magnetic materials.
-
Leaching (for Gold):
- Cyanidation: For gold extraction, the concentrated ore may undergo cyanidation, where it is treated with a cyanide solution to dissolve the gold. Activated carbon or zinc is then used to recover the dissolved gold from the solution.
- CIP/CIL: Carbon-in-pulp (CIP) or carbon-in-leach (CIL) processes can be used for the adsorption of gold onto activated carbon, followed by elution and electrowinning for final gold recovery.
-
Smelting and Refining:
- Gold Smelting: The gold-bearing carbon or precipitate is smelted in a furnace to produce gold bullion.
- Tin Smelting: The concentrated tin is heated in a reducing environment in a smelting furnace to produce tin metal.
- Both metals may undergo further refining to achieve the desired purity levels.
-
Tailings Management:
- Proper handling and disposal or storage of the tailings is crucial to minimize environmental impact. Tailings can sometimes be reprocessed to recover additional valuable minerals.
-
Quality Control and Monitoring:
- Throughout the process, rigorous quality control and monitoring are essential to ensure optimal recovery rates and concentrate quality. Samples are periodically taken and analyzed to make necessary adjustments to the process.
Each mining operation may have slight variations in the process based on the specific characteristics of the ore, the desired purity of the final product, and environmental considerations. Additionally, state-of-the-art technology and automation can enhance efficiency and safety in modern extraction plants.
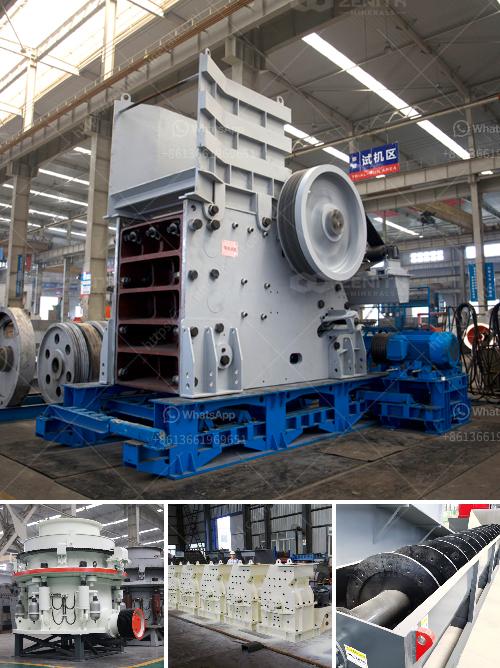