A 100tph coltan processing plant typically involves equipment and processes required to extract coltan (columbite-tantalite), which is a valuable mineral used in electronics. Here’s an overview of what such a plant might include:
Main Components:
-
Feeding System:
- Hopper: A container that holds raw coltan ore before it's processed.
- Vibrating Feeder: Feeds the raw material uniformly and continuously to the primary crusher or other processing machinery.
-
Crushing System:
- Jaw Crusher: Crushes large pieces of coltan ore into smaller fragments.
- Cone Crusher/Impact Crusher: Further reduces the size of the ore fragments.
-
Grinding System:
- Ball Mill/Rod Mill: Grinds the ore into finer particles.
- Classification Equipment: Such as a spiral classifier or hydrocyclone that separates fine particles from coarse ones.
-
Separation/Concentration System:
- Jig Separator: Utilizes gravity to concentrate coltan ore.
- Shaking Table: Separates fine coltan mineral particles by gravity.
- Magnetic Separator: Removes magnetic minerals, ensuring only coltan is processed.
-
Hydraulic Classifier/Spiral Chute:
- Further processes the ore slurry, separating minerals by density.
-
Dewatering System:
- Thickener: Concentrates slurry to remove water.
- Filter Press: Extracts remaining moisture from the ore concentrate.
Auxiliary Equipment:
- Conveyor Belts: Transports materials between different processing stages.
- Generator/Power Supply: Ensures continuous power for operation.
- Water Pump: Provides necessary water for washing and separating ore.
- Dust Collection System: Controls and removes dust generated during processing.
Operational Considerations:
- Capacity: 100tph (tons per hour) determines the scale of operations and choice of machinery.
- Environmental Compliance: Ensuring the plant adheres to environmental regulations, including proper waste disposal.
- Automation and Monitoring Systems: Implementing technology to enhance operational efficiency and safety.
Process Flow:
- Feeding and Crushing: Raw coltan ore is fed into the system, crushed, and ground to liberate coltan particles.
- Screening and Classification: Ground ore is classified by particle size, separating out fine particles for further processing.
- Gravity Separation: Concentrates coltan using gravity-based techniques like jigs and shaking tables.
- Magnetic Separation: Removes non-coltan materials using magnetic properties.
- Dewatering and Drying: Removes water, finalizing concentrate for sale or further refining.
Key Goals:
- Efficiency: Optimizing processing to maximize coltan yield.
- Purity: Ensuring the final product meets industry standards for coltan.
- Sustainability: Minimizing environmental impact and ensuring worker safety.
Such a plant would typically be designed by engineers and process experts, ensuring all components work harmoniously to achieve the desired output.
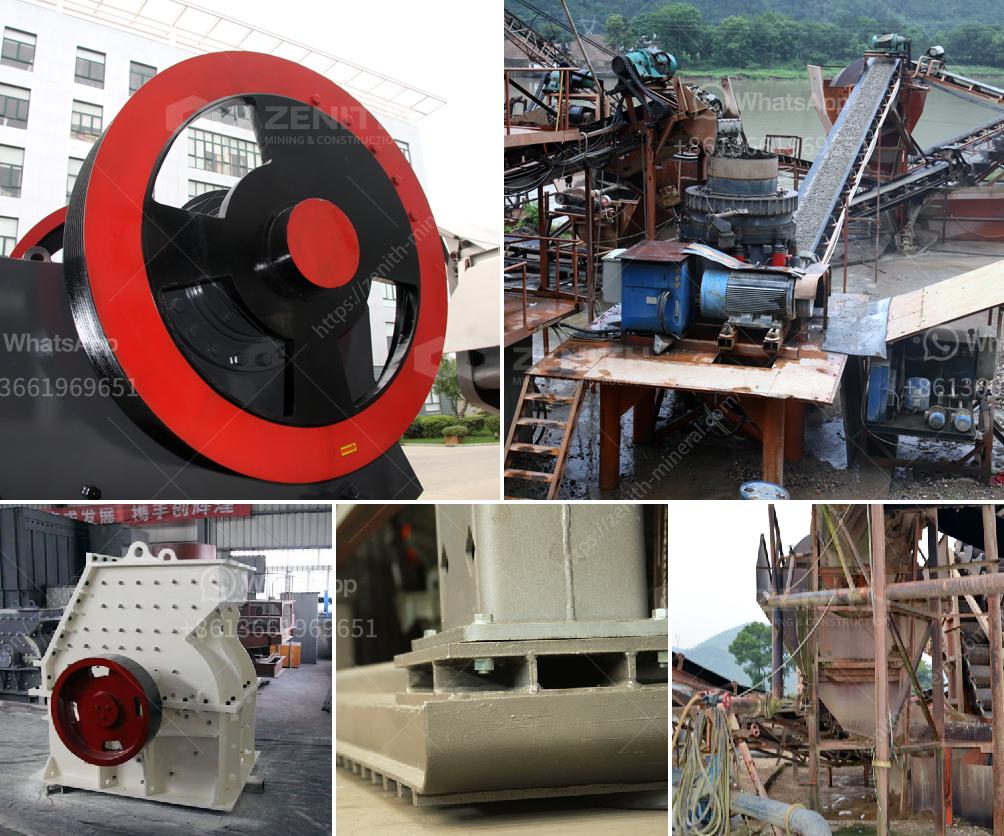