A hydraulic cone crusher is a type of machinery used for rock crushing in the mining and aggregate industries. Here’s a basic overview of how it operates:
-
Material Feeding:
- Raw materials are fed into the crusher via a hopper.
- The materials enter the crushing chamber, which is lined with a wear-resistant mantle and concave.
-
Hydraulic Adjustment:
- The hydraulic system allows precise adjustments to the crushing chamber setting.
- The system can raise or lower the mantle to change the distance between it and the concave, controlling the size of the output material.
-
Crushing Process:
- As the raw materials fall between the mantle and the concave, they are compressed, crushed, and reduced in size.
- The mantle oscillates via an eccentric bushing, causing it to gyrate. This action crushes the materials against the concave surface.
- The crushed material then exits through the bottom of the crusher once it reaches the desired size.
-
Hydraulic Protection:
- The hydraulic system also serves a protective role. If a non-crushable object (like a piece of metal) enters the crushing chamber, the hydraulic system can adjust to release the pressure, preventing damage to the crusher.
-
Automation and Control:
- Modern hydraulic cone crushers come equipped with automation systems that monitor operations, adjust settings, and ensure optimal performance and safety.
- Sensors track variables such as power consumption, temperature, and output size, automatically making adjustments as needed.
-
Lubrication and Cooling:
- Lubrication systems ensure that moving parts are properly greased, reducing wear and tear.
- Cooling systems maintain optimal operating temperatures, preventing overheating and prolonging the life of the machine.
In summary, a hydraulic cone crusher utilizes hydraulic mechanisms to adjust settings, provide protection, and enhance automation. It efficiently crushes materials through a combination of compression and controlled particle reduction, resulting in uniform and specified aggregate sizes.
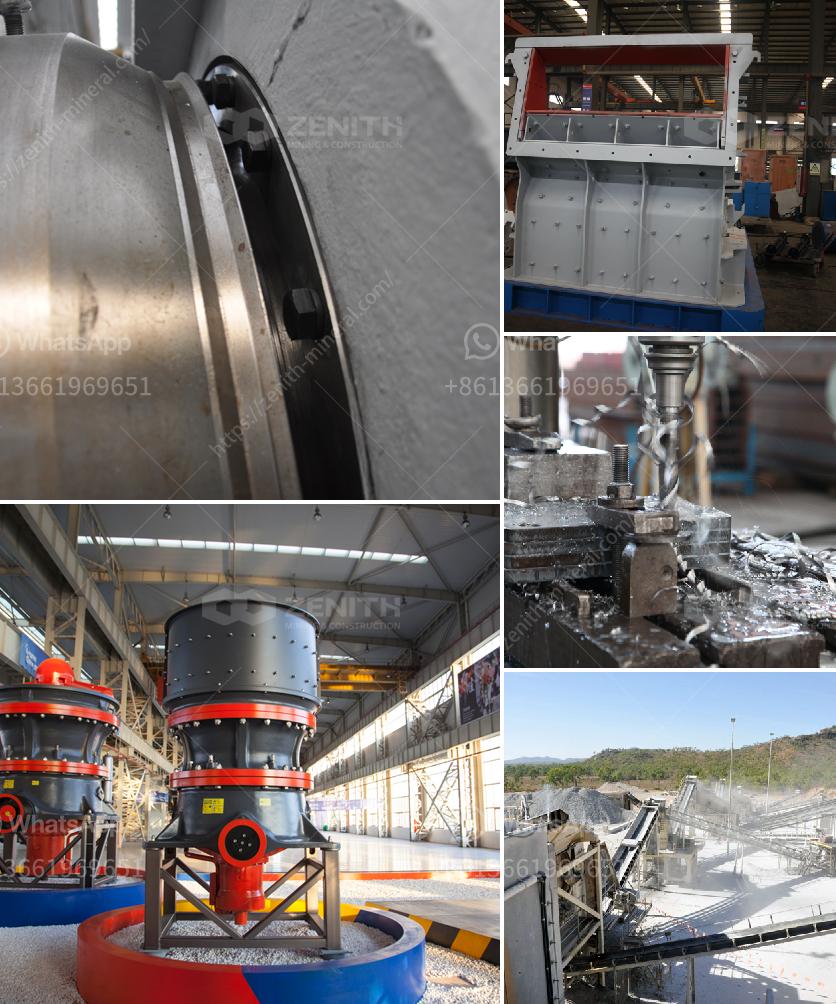