Nickel is commonly extracted from its ores using either pyrometallurgical or hydrometallurgical methods, depending on the nature of the ore and the desired purity of the final product.
-
Pyrometallurgical Method:
- Roasting and Smelting: Sulfide ores, such as pentlandite ((Fe,Ni)₉S₈), are typically concentrated via froth flotation and then roasted to convert sulfides into oxides. The roasted material is then smelted to remove impurities and produce a nickel-rich matte.
- Conversion to Pure Nickel: The nickel matte is further refined using converters to remove iron and sulfur, forming a nickel-copper matte. The final purification is done using techniques like the Mond Process, where carbon monoxide reacts with impure nickel to form nickel carbonyl (Ni(CO)₄) gas, which is then decomposed at high temperatures to produce high-purity nickel.
-
Hydrometallurgical Method:
- Leaching: Laterite ores, consisting mainly of nickel-bearing laterites like garnierite (a mixture of nickel and magnesium silicates), are processed using techniques like high-pressure acid leaching (HPAL) or heap leaching. This involves dissolving the nickel content into a solution using acids like sulfuric acid.
- Solvent Extraction and Electrowinning: Following leaching, the nickel is separated from the leach solution using solvent extraction techniques. The purified solution then undergoes electrowinning to deposit pure nickel onto cathodes.
-
Other Techniques:
- Bioleaching: In some cases, especially for processing lower-grade ores, biological methods involving bacteria to leach nickel from the ore can be used, though this is less common commercially.
The choice of extraction method largely depends on the ore type, economic considerations, and environmental impact.
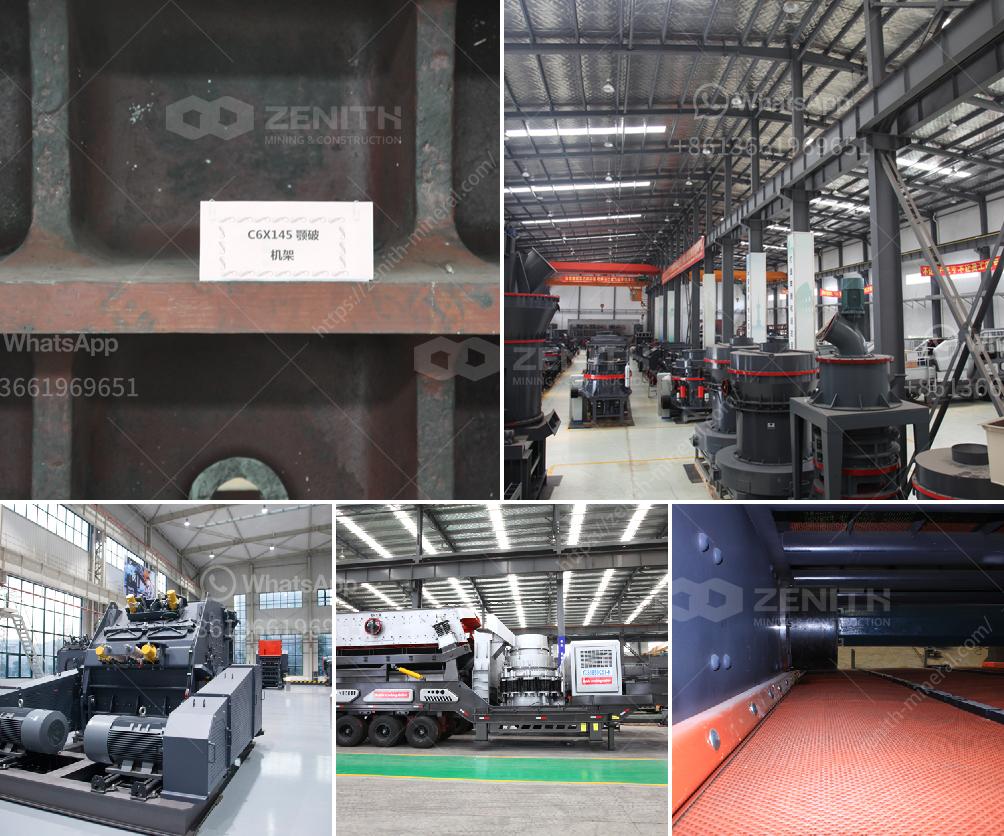