The process of extracting aluminium from its ore, bauxite, involves several key steps:
-
Mining of Bauxite: Bauxite is the primary ore of aluminium and it is composed mainly of aluminium oxide minerals such as gibbsite, boehmite, and diaspore. The bauxite ore is typically extracted through open-pit mining.
-
Crushing and Grinding: The extracted bauxite is transported to a processing facility where it is crushed into smaller particles and then ground into a fine powder.
-
Bayer Process:
- Digestion: The ground bauxite is mixed with a hot, concentrated solution of sodium hydroxide (NaOH). This reaction dissolves the aluminium-bearing minerals in the bauxite to form soluble sodium aluminate while leaving behind the impurities as an insoluble residue known as red mud.
- Clarification: The resulting mixture is allowed to settle, and the clear sodium aluminate solution is separated from the red mud.
- Precipitation: The sodium aluminate solution is cooled and seeded with aluminium hydroxide. This causes aluminium hydroxide to precipitate out of the solution.
- Calcination: The aluminium hydroxide precipitate is then heated in rotary kilns or fluidized bed calciners at temperatures up to 1000°C to remove water, resulting in the formation of anhydrous alumina (Al2O3).
-
Hall-Héroult Process: The production of aluminium metal from alumina involves the Hall-Héroult electrolytic process.
- Electrolysis: The alumina is dissolved in molten cryolite (Na3AlF6) in an electrolytic cell. A direct current is passed through the solution, causing the aluminium ions to migrate to the cathode where they are reduced to form aluminium metal, while oxygen is formed at the anode.
- Collection: The molten aluminium, being denser than the cryolite, settles at the bottom of the cell and is periodically siphoned off.
-
Casting and Rolling: The aluminium collected from the electrolytic cells is cast into ingots, billets, or other shapes, which can then be further processed by rolling, extruding, or other methods to produce various aluminium products.
This process is energy-intensive, particularly the electrolysis step, but it is essential for producing the high-purity aluminium used in a wide range of industries.
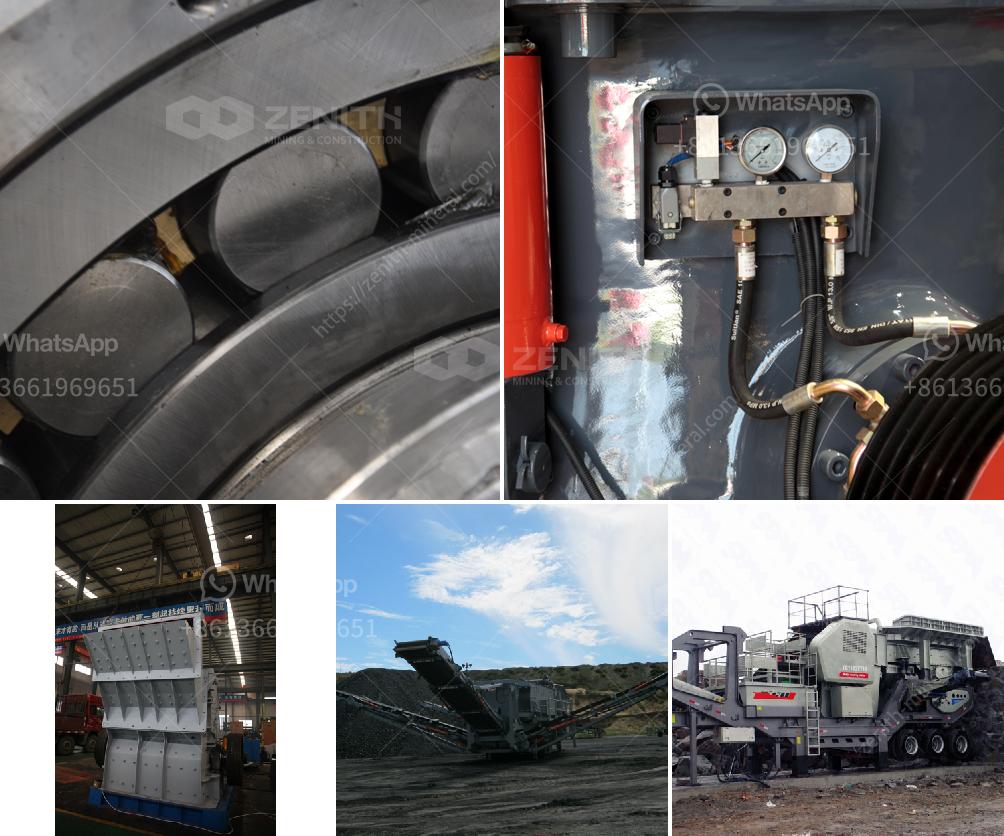