Manufacturing Portland cement involves several key steps, each crucial to producing a high-quality product. Here's an overview of the process:
-
Raw Material Extraction:
- Key raw materials include limestone, clay, and other materials such as sand and iron ore. These materials are typically extracted from quarries or mines.
-
Crushing and Grinding:
- The extracted raw materials are crushed to reduce them to smaller, more manageable sizes.
- They are then ground into a fine powder to prepare for the blending process.
-
Blending:
- The fine powders are proportioned and blended to create a uniform mixture. This mixture is crucial for producing a consistent product.
-
Preheating:
- The blended raw materials are fed into a preheater, which warms them using hot gases from the kiln. This step increases efficiency by reducing the amount of energy needed for heating in the kiln.
-
Kiln Phase:
- The preheated materials enter a rotary kiln, where they are heated to around 1450°C (2642°F). This intense heat causes chemical reactions that form clinker, small nodules of various compounds.
-
Clinker Cooling:
- The clinker exits the kiln and is rapidly cooled using air or water sprays to stabilize its structure and composition.
-
Grinding:
- The cooled clinker is mixed with a small amount of gypsum (to control the setting time of the final product) and then ground into a fine powder. This resulting product is Portland cement.
-
Storage and Packaging:
- The finished cement is stored in silos to protect it from moisture and contamination.
- It is then packaged into bags or shipped in bulk to customers.
By carefully controlling each of these steps, manufacturers can produce high-quality Portland cement suitable for a variety of construction applications.
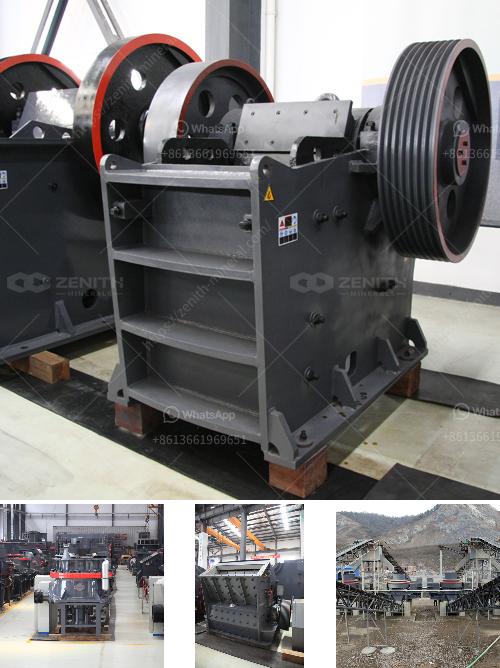