Crushers are essential pieces of equipment in the mining, construction, and recycling industries. Here's a brief overview of the differences between impact, cone, and jaw crushers:
-
Jaw Crusher:
- Mechanism: Uses compressive force; material is crushed between two rigid surfaces — a fixed and a moving jaw plate.
- Applications: Primarily used for the initial size reduction of larger rocks and materials. Suitable for hard and abrasive materials like granite and basalt.
- Output: Produces relatively coarse, irregularly shaped particles.
- Advantages: Simple structure, reliable operation, and easy maintenance.
-
Cone Crusher:
- Mechanism: Employs a gyrating spindle on which the crushing head (cone) cyclically approaches and withdraws from the fixed bowl (concave).
- Applications: Used for secondary, tertiary, or quaternary crushing stages. Ideal for medium to hard, abrasive materials.
- Output: Produces a more uniform particle size compared to jaw crushers; fine to medium granulation.
- Advantages: Good for fine crushing, consistent product shape, and efficiency. It also offers a high reduction ratio.
-
Impact Crusher:
- Mechanism: Uses impact force; material is repeatedly thrown against the impact plates and broken along natural crack lines.
- Applications: Commonly used for soft to medium-hard materials like limestone, coal, and gypsum. Suitable for recycling applications.
- Output: Produces well-graded particles with a superior shape and consistency. The output size can be adjusted by changing the rotor speed and the clearance between impact plates.
- Advantages: High reduction ratios, effective for shaping, and can produce multiple products in a single pass.
Summary: Jaw crushers are typically used for primary crushing stages and are well-suited to handle hard, abrasive materials. Cone crushers are usually implemented for secondary or further reduction stages, providing uniform shapes and fine crushing capabilities. Impact crushers, on the other hand, are versatile tools best used in scenarios where particle shape is crucial and for recycling materials, offering high reduction ratios and efficient material processing.
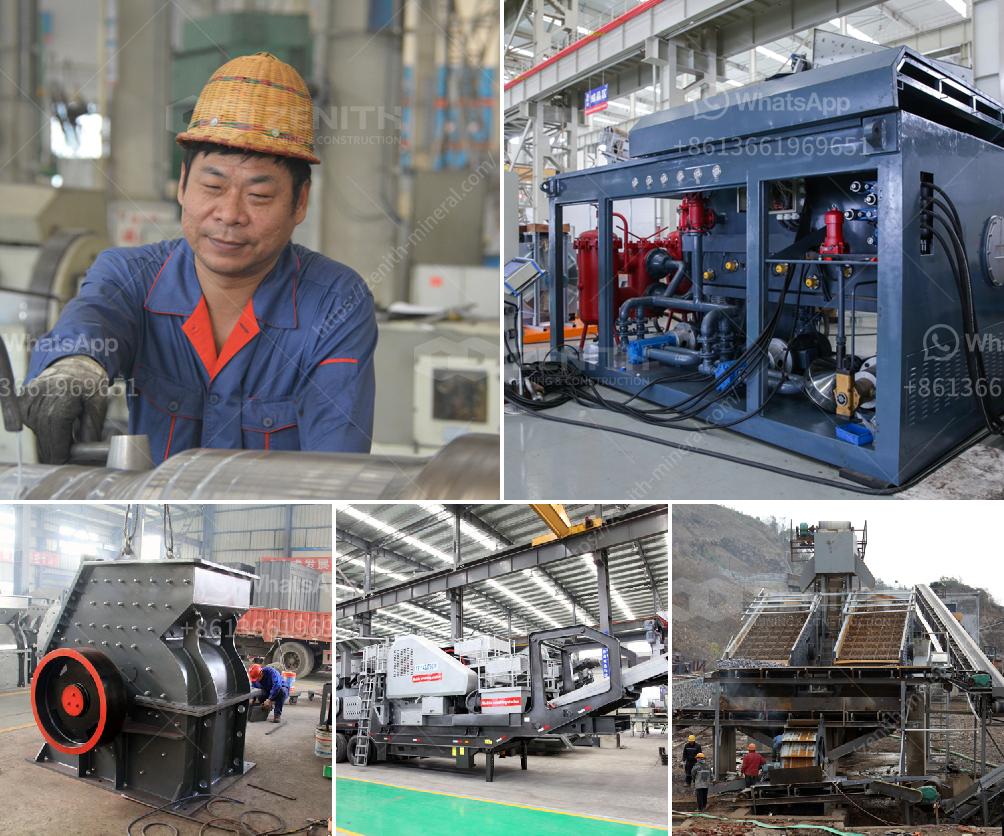