Both impact crushers and cone crushers are essential machinery in aggregate production and mineral processing, but they operate and are used in different ways. Here's a breakdown of their differences:
1. Crushing Mechanism:
- Impact Crusher: Utilizes impact force to crush materials. When materials enter the crusher, they are hit by blow bars in a high-speed rotor, leading to fragmentation. The crushed material then strikes stationary plates (anvils or breaker plates) and further disintegrates.
- Cone Crusher: Relies on compression crushing. The material is placed between a moving piece of steel (the mantle) and a stationary piece (the concave), which compresses it until it breaks.
2. Feed Material:
- Impact Crusher: Suitable for softer, less abrasive stones such as limestone. It’s also well-suited for recycling concrete and asphalt.
- Cone Crusher: Better for harder, more abrasive materials like granite and basalt. It is also ideal for secondary, tertiary, and quaternary crushing stages.
3. Efficiency and Output:
- Impact Crusher: Offers high reduction ratios and the ability to produce a uniform cubical product. However, it may generate more fines and dust.
- Cone Crusher: Provides consistent, high-quality end products and can handle a wide range of material hardness. It is generally more efficient in producing high-quality aggregates with fewer fines.
4. Maintenance and Wear Parts:
- Impact Crusher: Typically has higher wear rates and requires frequent replacement of wear parts like blow bars and impact plates.
- Cone Crusher: Usually has lower wear costs over time. Parts like liners and mantles are generally more durable.
5. Adjustability:
- Impact Crusher: Easier and quicker to adjust to achieve different output sizes.
- Cone Crusher: Adjustments can be made through mechanical means, but it may not be as rapid as with an impact crusher.
6. Energy Consumption:
- Impact Crusher: Generally consumes more energy per ton of material processed due to the high-speed impact mechanism.
- Cone Crusher: More energy-efficient, using lower operating speeds and providing better power utilization.
Understanding these differences can help you select the appropriate crusher for your specific application, ensuring optimal performance and efficiency.
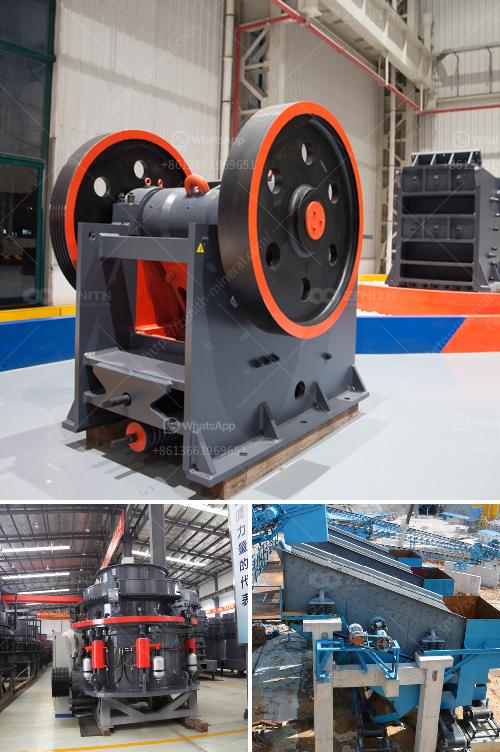