Choosing a vibrating feeder involves several key considerations to ensure it meets your specific needs and application requirements. Here’s a step-by-step guide to help you make an informed decision:
-
Material Characteristics:
- Type of material: Consider the type of material (granular, powder, aggregate) you will be moving.
- Material properties: Look at factors such as bulk density, moisture content, particle size, and abrasiveness.
-
Capacity and Throughput:
- Determine the amount of material that needs to be moved per unit time.
- Match the feeder size and capacity with your required throughput rates.
-
Mounting Options:
- Decide whether you need a suspension or base-mounted feeder.
- Consider the space available for installation and how the feeder will integrate with your existing equipment.
-
Feeding Mechanism:
- Choose between an electromagnetic or electromechanical feeder depending on your application's needs.
- Electromagnetic feeders are more controllable, suitable for precise feeding, while electromechanical feeders are typically more robust, handling heavier loads.
-
Power Requirements:
- Check the power requirements and ensure it matches your facility's power supply.
- Consider energy efficiency for cost-effective operation.
-
Control Features:
- Look for feeders with adjustable feed rates and control options to suit your operational needs.
- Advanced models may offer digital controls for precise feed regulation.
-
Construction and Durability:
- Ensure the construction materials of the feeder can withstand the operating environment.
- Stainless steel is commonly chosen for its durability and resistance to corrosion.
-
Ease of Maintenance:
- Choose a feeder that is easy to maintain and has readily available spare parts.
- Consider the design in terms of cleaning and wear part replacement access.
-
Noise and Vibration Levels:
- Assess the noise and vibration levels the feeder produces, ensuring they are compatible with your facility’s requirements for a safe and comfortable working environment.
-
Cost:
- Balance the initial investment with long-term operational costs.
- Consider not only the purchase price but also the potential benefits in productivity and reduced maintenance costs.
-
Manufacturer Support and Reputation:
- Opt for a reputable manufacturer who offers good customer support, warranties, and after-sales service.
- Check reviews, case studies, or references from other users in your industry.
By carefully considering these factors, you can select a vibrating feeder that optimally fits your operational needs and ensures efficient, reliable material handling.
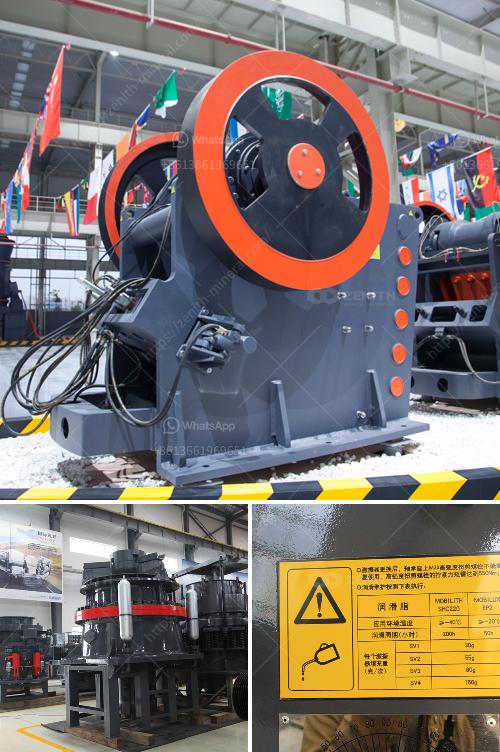