Iron ore mining is a complex process that involves several steps to extract and process the material. Here's an overview of how it is typically conducted:
1. Exploration and Evaluation
- Geological Survey: Geologists conduct surveys to identify regions rich in iron ore deposits. This may involve mapping, sampling, and geophysical methods.
- Drilling: Exploratory drilling is done to obtain samples from below the earth’s surface to analyze the quality and quantity of the ore.
2. Planning and Development
- Feasibility Study: A detailed assessment of the ore body and economic viability is conducted, including environmental impact studies.
- Mine Design: Once a site is deemed profitable, engineers design the layout of the mine which includes roads, facilities, and infrastructure.
3. Extraction
- Open-Pit Mining: Involves removing layers of earth to reach ore deposits near the surface. This is the most common method.
- Underground Mining: Used for deeper deposits, where shafts and tunnels are created to reach and extract the ore.
4. Blasting and Digging
- Blasting: Controlled explosions are used to break up the rock and access the ore.
- Excavation: Heavy machinery, such as excavators and loaders, are used to move the broken ore to transport vehicles.
5. Transportation
- Haul Trucks: Large trucks transport the ore from the mine site to screening and crushing facilities.
- Conveyors and Rail: In some cases, conveyors or rail systems are used for more efficient long-distance transport.
6. Crushing and Screening
- Primary Crushing: The ore is crushed into smaller pieces to facilitate easier transportation.
- Screening: The crushed ore is screened to separate it into various sizes for further processing.
7. Beneficiation
- Grinding: The ore is ground to a fine powder to liberate the iron particles from the surrounding material.
- Magnetic Separation: Magnets are used to separate iron ore from waste rock.
- Flotation: Chemicals are added to a slurry of ground ore to make the iron particles float, making it easier to separate.
8. Pelletizing (Optional)
- The iron powder is processed into pellets to improve handling and reduce dust during transport and smelting.
9. Smelting
- Blast Furnace: The iron ore pellets or fines are heated in a blast furnace with coke and limestone to produce molten iron, which is then further refined into steel.
10. Environmental Management
- Reclamation: Once mining activities are complete, efforts are made to restore the land to its natural state.
- Water Treatment: Used water from mining processes is treated to remove contaminants before being released back into the environment.
- Dust Control: Measures are taken to reduce dust at the mining site, such as using water sprays and vegetation barriers.
11. Monitoring and Compliance
- Regular Inspections: Ongoing monitoring of the mining operations and their environmental impact to ensure compliance with regulations.
Iron ore mining is an industry that requires careful planning, efficient execution, and strict adherence to environmental and safety regulations to ensure sustainable operations.
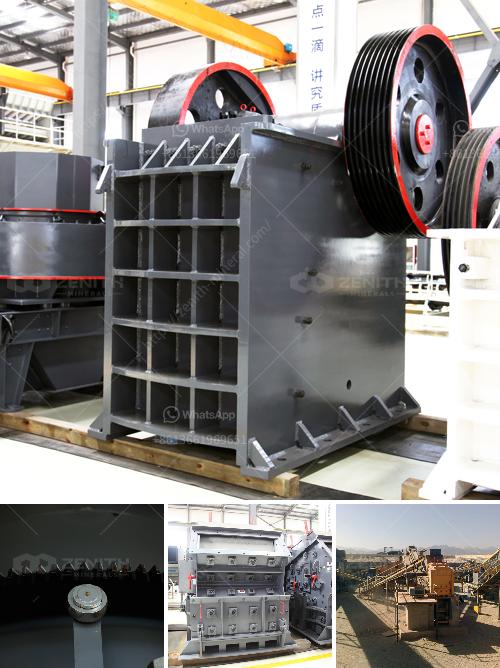