Sizing grinding mills involves several important considerations to ensure optimal performance and efficiency. Here’s a general overview of the key steps:
1. Identify Material Properties
- Hardness: Determine the hardness of the material, as this influences the type of mill and grinding media required.
- Granulometry: Assess the particle size distribution of the feed material.
- Moisture Content: Check the moisture content because it can affect both the choice of mill and operational conditions.
- Bulk Density: Know the bulk density to help in mill sizing calculations.
2. Define Desired Product Specifications
- Final Particle Size: Specify the required fineness of the final product.
- Specific Surface Area: Understand requirements related to the surface area of the milled product.
- Production Rate: Establish the desired throughput or production capacity.
3. Mill Selection
- Mill Types: Compare different types of mills (e.g., ball mills, vertical roller mills, SAG mills, etc.) depending on the material and end goals.
- Energy Efficiency: Consider mills that offer higher energy efficiency for cost and environmental benefits.
4. Perform Grinding Tests
- Conduct laboratory or pilot-scale grinding tests to acquire empirical data on material behavior under grinding.
- Use the test results to develop grindability indices (e.g., Bond Work Index).
5. Calculate Mill Dimensions and Power
- Mill Diameter and Length: Use empirical formulas and design algorithms, such as the Bond method, to calculate the required mill diameter and length.
- Power Requirements: Determine the horsepower required to achieve the desired grinding performance using specific energy consumption data.
6. Consider Mill Liners and Grinding Media
- Liner Design: Choose appropriate liner designs to optimize grinding efficiency and mill life.
- Grinding Media: Select the appropriate size, material, and quantity of grinding media (e.g., steel balls in a ball mill).
7. Operational Factors
- Feed Rate: Regulate the feed rate to ensure consistent mill performance.
- Mill Speed: Adjust the mill speed to align with the optimal grinding conditions.
- Load and Circulation: Optimize the circulating load and material hold-up within the mill.
8. Scale-Up Considerations
- When transitioning from pilot to full-scale production, employ scale-up principles to account for geometric, kinematic, and dynamic similarities.
9. Vendor Consultation
- Engage with equipment manufacturers early in the design process to leverage their expertise and recommendations.
10. Regulatory and Safety Considerations
- Comply with any relevant industry standards and safety regulations during design, installation, and operation.
Consulting with a mechanical or process engineer specialized in comminution can also provide valuable insights tailored to your specific project requirements.
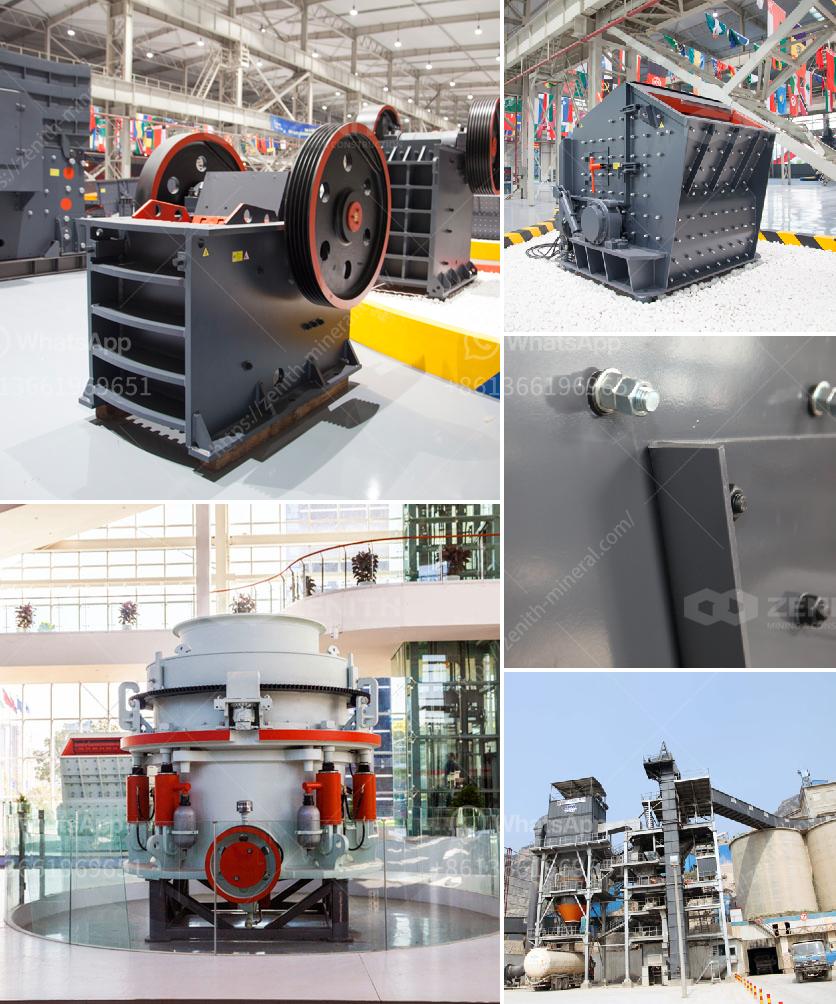