Designing a crushing plant involves various steps and considerations to ensure high efficiency, safety, and cost-effectiveness. Here’s a general guide to help you design a crushing plant:
1. Define Objectives and Requirements
Objectives:
- Determine the desired output size and production capacity.
- Decide on the material types and properties, such as hardness and abrasiveness.
Requirements:
- Compliance with environmental and local regulations.
- Budget constraints and available resources.
2. Site Selection and Layout
Site Conditions:
- Evaluate the topography and soil conditions of the site.
- Ensure adequate space for equipment, stockpiles, and operational areas.
Layout:
- Plan the location of the crusher, stockpiles, conveyor belts, and other facilities.
- Design a layout that minimizes material handling and reduces transport distances.
3. Equipment Selection
Primary Crusher:
- Choose between a jaw crusher, gyratory crusher, or impact crusher based on the material’s hardness and the desired reduction ratio.
Secondary and Tertiary Crushers:
- Select cone crushers, impact crushers, or gyratory crushers depending on the secondary processing requirements.
Screening and Conveying:
- Include vibrating screens, feeders, and conveyor systems to separate and transport materials effectively.
4. Capacity Planning
Throughput:
- Calculate the required capacity for each stage of the crushing process.
- Ensure the equipment selected can handle peak loads and operational variability.
Redundancy:
- Design for redundancy in critical equipment to minimize downtime.
5. Energy Efficiency
Power Supply:
- Ensure a reliable power source to handle the energy demands of the plant.
Energy-Saving Measures:
- Incorporate energy-efficient motors and variable frequency drives.
- Opt for automated control systems to optimize crushing operations.
6. Safety and Environmental Considerations
Dust and Noise Control:
- Implement dust suppression systems, such as water sprays and dust collectors.
- Design noise barriers and use quieter equipment to reduce noise pollution.
Environmental Impact:
- Conduct environmental impact assessments.
- Plan for proper waste management and recycling options.
7. Automation and Monitoring
Automation:
- Utilize automated control systems for real-time monitoring and adjustments.
- Implement automated lubrication and maintenance alerts.
Monitoring:
- Install sensors and cameras to monitor equipment performance and material flow.
- Use data analytics to predict maintenance needs and optimize operations.
8. Maintenance and Operations Plan
Routine Maintenance:
- Develop a maintenance schedule including daily checks, lubrication, and part replacements.
Operational Training:
- Train personnel on the operation, safety protocols, and emergency procedures.
Spare Parts Inventory:
- Maintain an inventory of critical spare parts to reduce downtime.
9. Testing and Commissioning
Initial Testing:
- Perform initial test runs to ensure all equipment works as planned.
- Make adjustments based on the test results.
Commissioning:
- Conduct final checks and commissioning procedures.
- Validate operational efficiency and compliance with design specifications.
10. Documentation and Continuous Improvement
Documentation:
- Keep detailed records of design plans, maintenance schedules, and operational data.
Continuous Improvement:
- Regularly review performance data to identify areas for improvement.
- Implement updates and modifications as necessary to enhance efficiency and productivity.
By following these steps, you can design a crushing plant that meets your production needs while ensuring safety, efficiency, and environmental compliance.
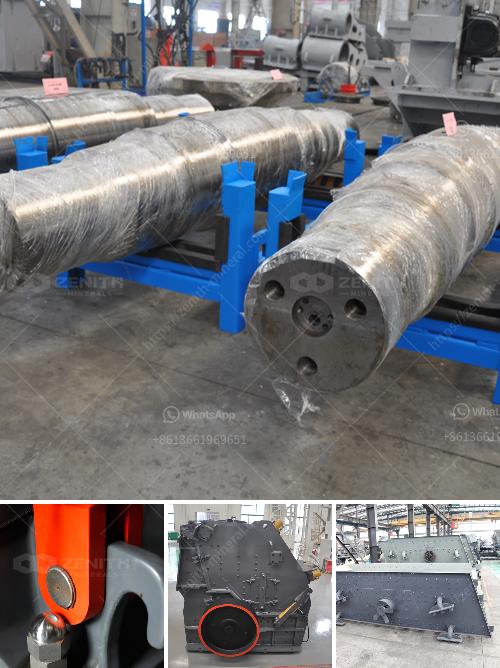