When looking at small jaw crushers versus cone crushers for sale, there are several key differences in their design, operation, and suitability for different applications:
-
Design and Operation:
- Jaw Crushers: These are typically used as primary crushers. They are designed to crush material by compressing it between a fixed plate and a moving plate. The feed material is reduced in size as it moves downwards through the chamber until it is small enough to pass through the bottom opening.
- Cone Crushers: Used as secondary or tertiary crushers, cone crushers crush material by squeezing or compressing it between a manganese concave and a gyrating cone. The crushed material is then discharged from the bottom of the machine.
-
Usability:
- Jaw Crushers: Ideal for primary stage crushing, suitable for hard and abrasive materials. They are widely used in mining and demolition recycling.
- Cone Crushers: Typically used for secondary, tertiary, or quaternary crushing stages. They are more suitable for medium to hard, abrasive materials and are often used in aggregate production.
-
Output Size:
- Jaw Crushers: Generally produce a more irregular and larger particle size, which might require secondary crushing.
- Cone Crushers: Provide a more consistent and finer end-product size, suitable for processes where precise particle size is important.
-
Capacity and Efficiency:
- Jaw Crushers: Usually have a lower capacity than cone crushers and may be less efficient at producing finer materials.
- Cone Crushers: Typically offer higher capacity and better efficiency, particularly for finer materials.
-
Maintenance:
- Jaw Crushers: Require less complex maintenance due to their simpler mechanical structure. However, the wear and tear on the jaw plates are significant.
- Cone Crushers: Generally have more complex structures and thus may require more maintenance to ensure optimal performance. Regular inspection and replacement of wear parts are necessary.
-
Mobility:
- Jaw Crushers: Often available in both fixed and mobile configurations, making them versatile for different site conditions.
- Cone Crushers: Also available as mobile units, but primarily found in stationary configurations due to their weight and the nature of their crushing mechanism.
-
Applications:
- Jaw Crushers: Best for use in rock quarries where large materials need to be broken down.
- Cone Crushers: Often used for detailed rock shaping and in applications requiring smaller, precise material sizes, like sand and gravel production.
When choosing between a small jaw crusher and a cone crusher, consider the material type, size, and end-use, as well as the capacity and production requirements of the operation.
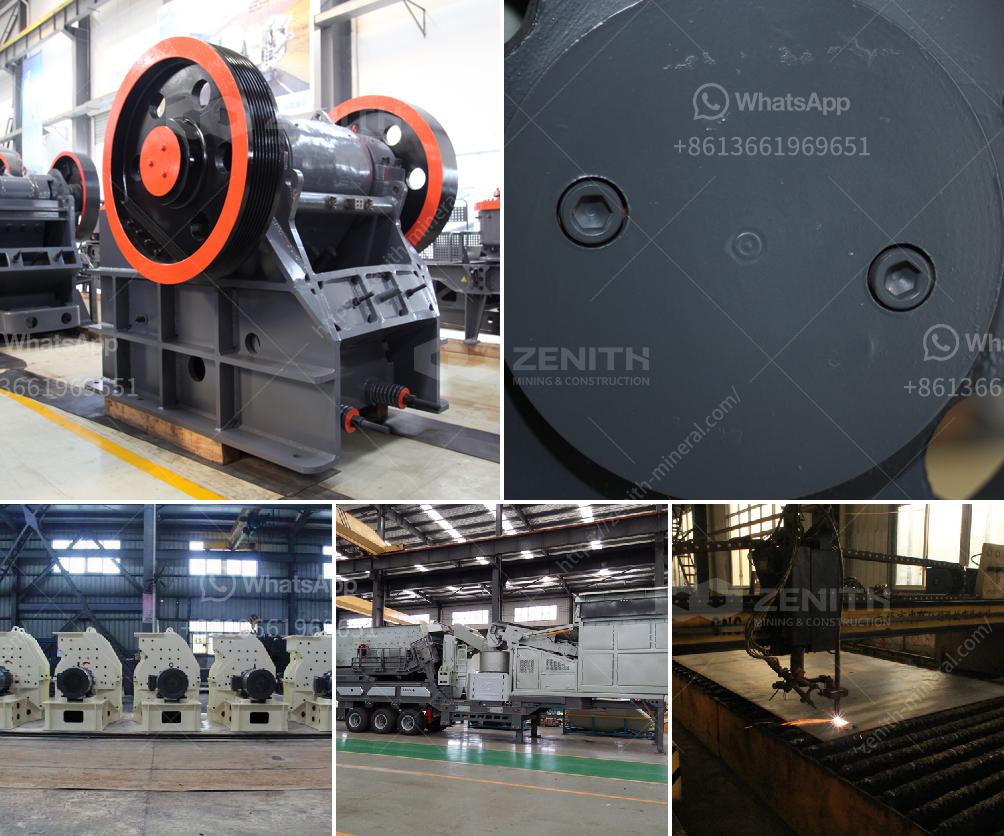