Manufacturing a mobile crusher with a capacity of 250 tons per hour (tph) involves several steps, including design, material selection, assembly, and testing. Here’s an overview of the process:
-
Design and Engineering:
- The first step in manufacturing a mobile crusher is the design phase, where engineers create detailed blueprints and models. They consider aspects such as size, capacity (250 tph in this case), power source, mobility, and the materials to be crushed.
- Computer-aided design (CAD) software is typically used to model and simulate the crusher's components and performance.
-
Material Selection:
- Choosing the right materials is crucial for durability and efficiency. High-quality steel and wear-resistant materials are often used for components such as jaws, impact plates, and cones.
- Considerations for materials also include corrosion resistance and the ability to handle the stress and wear associated with crushing high volumes of material.
-
Component Manufacturing:
- Fabrication of the crusher’s major components—like the frame, crushing chamber, conveyors, motors, and control systems—takes place in specialized facilities.
- Precision machining tools are used to cut, shape, and prepare these components according to the design specifications.
-
Assembly:
- Components are assembled into the main unit, which includes installing the jaws or cones, power units, conveyors, and control panels.
- The integration of hydraulic and electrical systems is done during assembly, ensuring that all moving parts function together smoothly.
-
Quality Control and Testing:
- Once assembled, the mobile crusher unit undergoes rigorous quality control checks. This includes checking alignments, weld integrity, and component securement.
- The crusher is then tested for functionality by running it under load to verify that it can efficiently process 250 tons of material per hour without issues.
-
Mobility Features:
- Since these crushers are mobile units, manufacturing includes adding tracks or wheels for transportability. This requires robust construction to handle movement over various terrains.
- Systems for easy setup and tear-down are integrated, making it efficient to move the crusher between job sites.
-
Final Adjustments and Finishing:
- After testing, any necessary adjustments are made to optimize performance. This might include tuning software settings for automated systems or making mechanical tweaks.
- Protective coatings or paint are applied to protect against environmental factors and wear.
-
Packaging and Shipping:
- The final step is preparing the mobile crusher for shipment, which includes further quality checks and secure packaging methods to prevent damage during transport to the client site or dealer.
Throughout the process, manufacturers must adhere to stringent safety and environmental standards to ensure the end product is safe to operate and environmentally friendly.
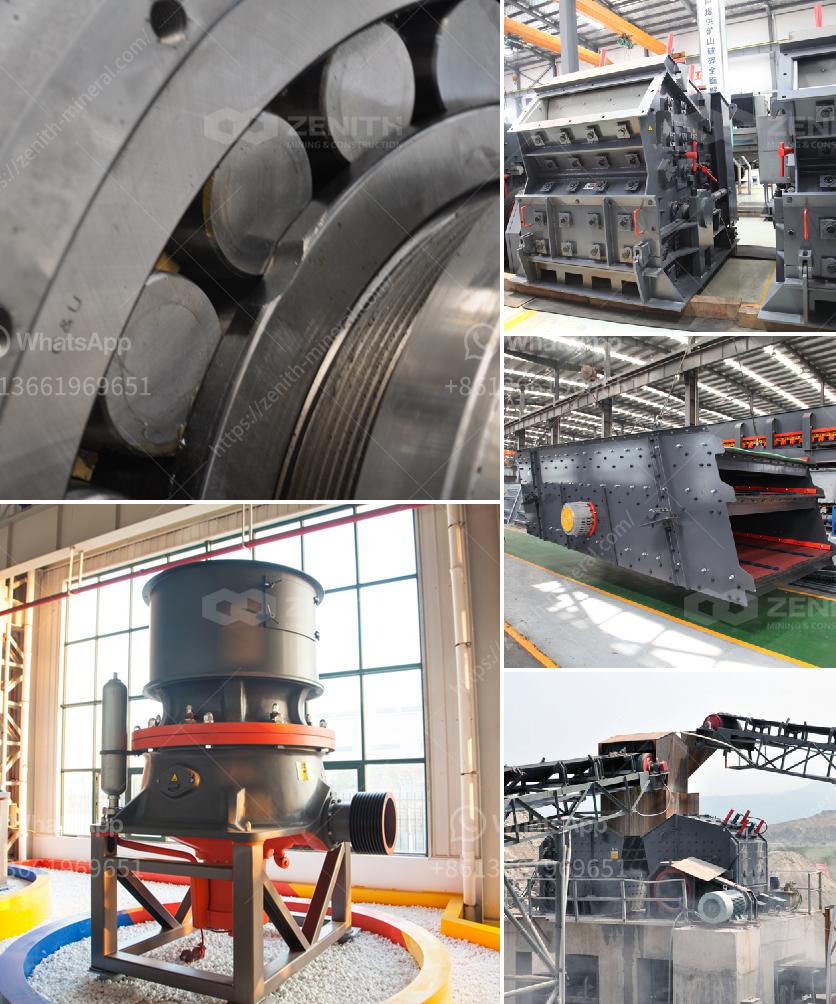