Crushers are machines used to reduce the size of rocks, stones, and ore for various industrial applications. They differ in their design, operation, and the nature of the materials they can handle. Here are three common types of crushers and how they differ:
-
Jaw Crushers:
- Design and Operation: Jaw crushers consist of two platens, one movable and the other fixed. Rocks are crushed between these platens as the movable jaw compresses against the fixed one.
- Material Handling: They are typically used for primary crushing of large rocks and are able to handle hard and abrasive materials like granite and ores.
- Output Characteristics: Produces relatively coarse output size and can handle large input material sizes.
-
Cone Crushers:
- Design and Operation: Cone crushers use a gyrating spindle in a conical chamber to compress rocks against the chamber wall. The reduction occurs from repeated squeezing as the spindle rotates eccentrically within the fixed outer shell.
- Material Handling: Suitable for secondary, tertiary, and fine crushing stages. They handle medium-hard to very hard materials, like basalts and granites.
- Output Characteristics: Provide fine and consistent output size and shape, which makes them ideal for creating road base material.
-
Impact Crushers:
- Design and Operation: Impact crushers use impact forces to break material. A rotor spins against pieces of material, propelling them against breaker plates to shatter upon impact.
- Material Handling: Best for softer or medium-hard materials, like limestone and gypsum. Ideal for recycling concrete and asphalt.
- Output Characteristics: Achieves varied levels of reduction and can produce highly uniform cubical particle shapes, but with somewhat higher fines production.
Each type of crusher has its unique strengths and is selected based on the specific material characteristics, the stage of the crushing process, and the output requirements.
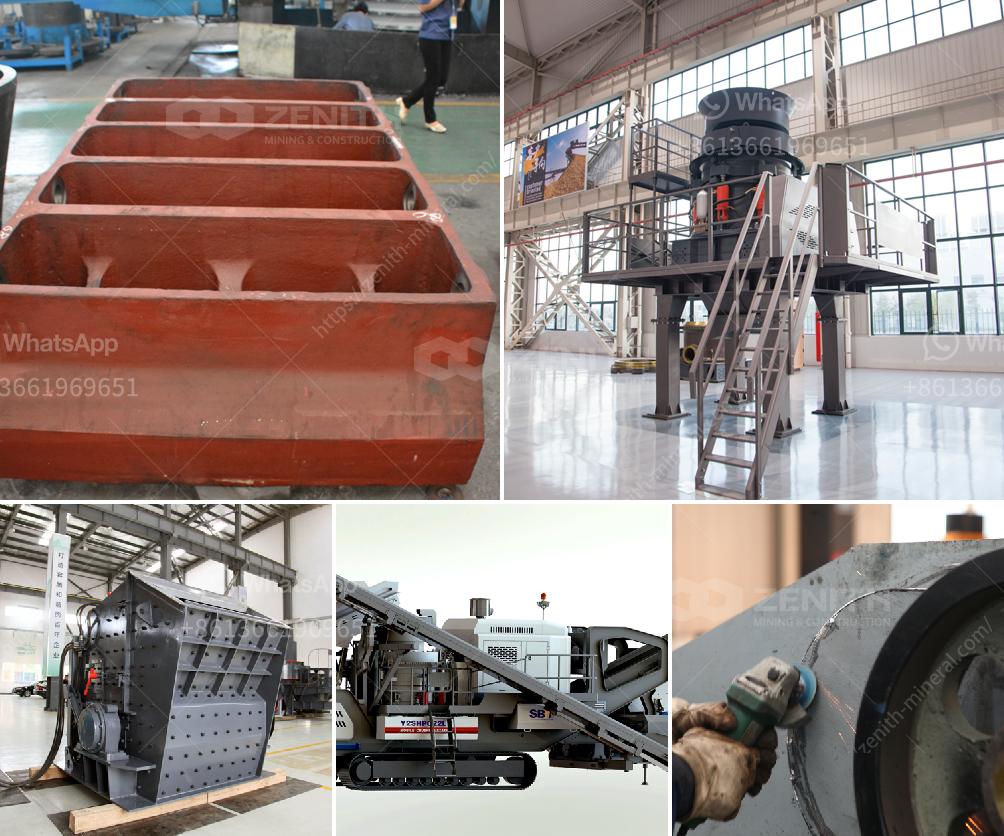