Starting a ballast crushing plant involves several steps, including planning, obtaining necessary permits, setting up the plant, and ensuring efficient operation. Here’s a detailed guide to help you get started:
1. Feasibility Study and Business Plan
- Market Research: Conduct thorough market research to understand the demand for ballast in your target area. Identify potential customers, such as construction companies and railway operators.
- Feasibility Study: Assess the feasibility of the project, including the availability of raw materials (stone), transportation logistics, and financial viability.
- Business Plan: Develop a comprehensive business plan outlining your business model, target market, marketing strategy, operational plan, and financial projections.
2. Legal and Regulatory Requirements
- Permits and Licenses: Obtain the necessary permits and licenses from local, state, and federal authorities. This may include environmental permits, land use permits, and business licenses.
- Environmental Impact Assessment (EIA): Conduct an EIA to assess the potential environmental impacts of your plant and develop mitigation measures.
3. Site Selection and Preparation
- Location: Choose a suitable location for your plant, considering factors such as proximity to raw material sources, transportation infrastructure, and market access.
- Land Acquisition: Acquire the land for your plant, ensuring it meets zoning and land use regulations.
- Site Preparation: Prepare the site by clearing vegetation, leveling the ground, and constructing access roads.
4. Plant Design and Equipment Selection
- Plant Design: Design the layout of your plant, including the placement of crushers, screens, conveyors, and storage areas.
- Equipment Selection: Select the appropriate crushing and screening equipment based on the type and size of the raw material, production capacity, and desired product specifications. Common equipment includes jaw crushers, cone crushers, impact crushers, and vibrating screens.
5. Installation and Commissioning
- Equipment Installation: Install the crushing and screening equipment according to the manufacturer’s instructions. Ensure all components are properly aligned and securely fastened.
- Electrical and Plumbing: Set up the electrical and plumbing systems to power the equipment and provide water for dust suppression.
- Commissioning: Test the equipment to ensure it operates correctly and meets production specifications. Make any necessary adjustments to optimize performance.
6. Operations and Maintenance
- Staffing: Hire and train staff to operate and maintain the plant. This includes machine operators, maintenance technicians, and quality control personnel.
- Operational Procedures: Develop standard operating procedures (SOPs) for all aspects of the plant’s operation, including safety protocols, equipment operation, and quality control.
- Maintenance Plan: Implement a preventive maintenance plan to ensure the equipment remains in good working condition and minimize downtime.
7. Marketing and Sales
- Marketing Strategy: Develop a marketing strategy to promote your ballast products to potential customers. This may include advertising, attending trade shows, and building relationships with construction companies and railway operators.
- Sales Channels: Establish sales channels, such as direct sales, distributors, and online platforms, to reach your target market.
8. Continuous Improvement
- Quality Control: Implement a quality control system to ensure your ballast meets industry standards and customer specifications.
- Customer Feedback: Gather feedback from customers to identify areas for improvement and enhance your products and services.
- Innovation: Stay updated on industry trends and technological advancements to continuously improve your plant’s efficiency and product quality.
By following these steps, you can successfully start and operate a ballast crushing plant. Remember to stay compliant with all legal and regulatory requirements and continuously seek ways to improve your operations.
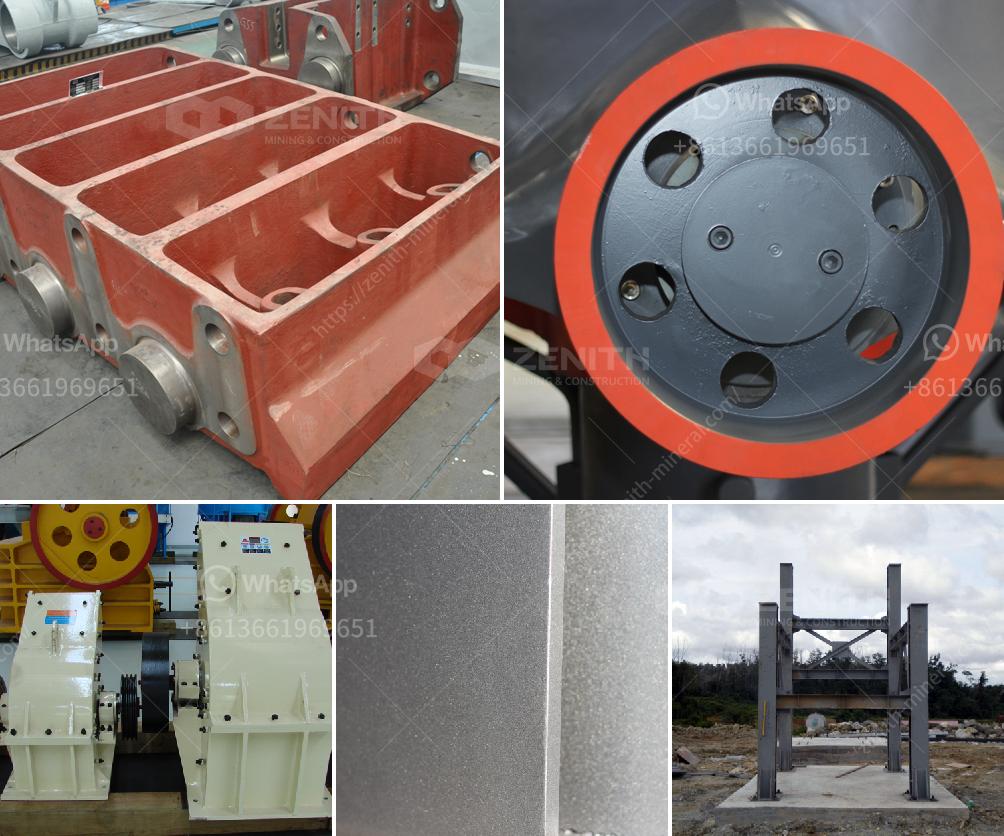