Separating gold from iron ore typically involves several processes. Here’s a simplified overview of the methods commonly used:
1. Crushing and Grinding
- Crushing: The ore is first crushed to break it into smaller pieces.
- Grinding: The crushed ore is then ground to a fine powder to liberate the gold particles.
2. Concentration
- Gravity Separation: Since gold is denser than iron, gravity-based methods like shaking tables, sluice boxes, or centrifugal concentrators can be used to separate gold particles from the lighter material.
- Flotation: Chemicals are added to create a froth that selectively binds to gold particles, lifting them to the surface where they can be skimmed off.
3. Amalgamation
- Mercury Amalgamation: Mercury is mixed with the ore to form an amalgam with gold, because gold readily bonds with mercury while iron does not. The amalgam is then heated to evaporate the mercury, leaving behind pure gold. However, this method is hazardous due to mercury's toxicity and environmental impact.
4. Cyanidation
- Cyanide Leaching: The powdered ore is treated with a cyanide solution, which dissolves the gold. The solution is then processed to recover the gold through precipitation (often using zinc) or by using activated carbon.
5. Electromagnetic Separation
- Electromagnetic Methods: Since iron is magnetic and gold is not, magnetic separation can sometimes be used to remove iron particles from the ore.
6. Refining
- Melting and Refining: The concentrated gold is often heated until it melts. The molten gold is poured into a mold to form bars, which can then be further refined to achieve higher purity levels.
Safety and Environmental Considerations
- Always follow safety guidelines and regulations.
- Consider the environmental impact of the chosen method, especially when using chemicals like mercury and cyanide.
By selecting the appropriate combination of these methods based on the specific nature of the ore, it is possible to efficiently separate gold from iron ore.
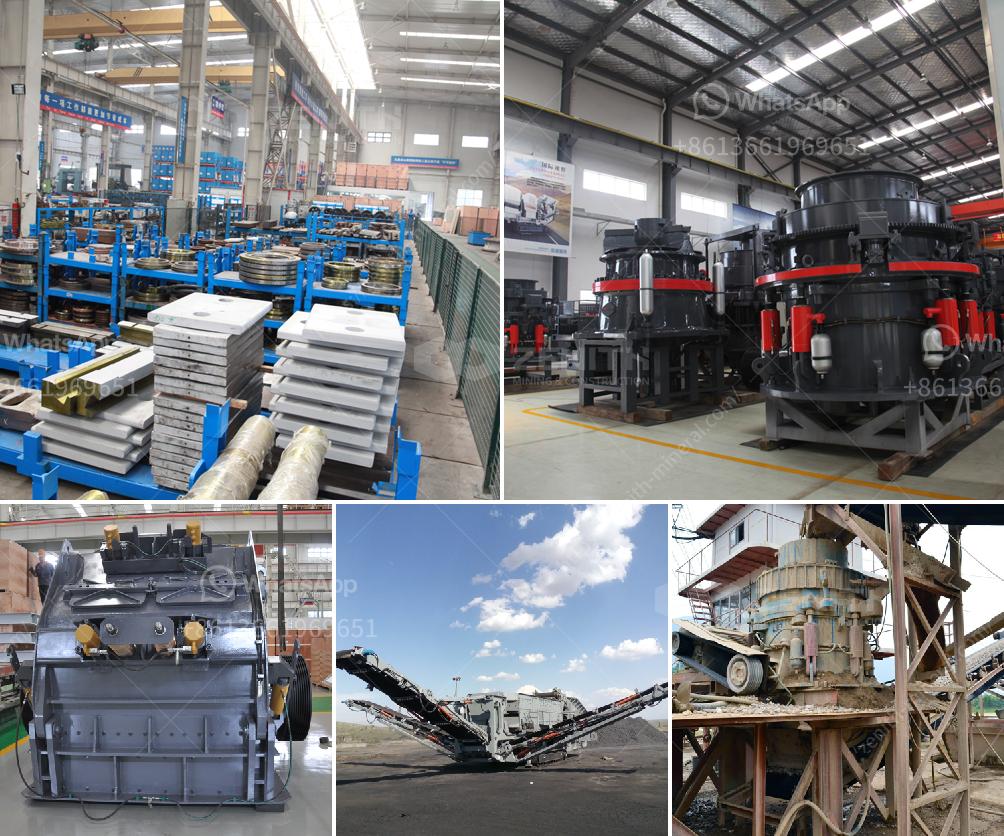