To make cement powder using a ball mill, you need to follow a series of steps that involve the preparation of raw materials, the grinding process, and the final production of the cement powder. Here is a detailed guide on how to achieve this:
1. Raw Material Preparation
Materials Needed:
- Limestone
- Clay
- Sand
- Iron ore
These materials are the primary components used in the production of cement. They need to be carefully selected and prepared before being fed into the ball mill.
2. Crushing and Pre-homogenization
Crushing:
- The raw materials are crushed into small pieces using crushers. This step is crucial to ensure that the materials are of a uniform size, which facilitates the grinding process.
Pre-homogenization:
- The crushed materials are then mixed and homogenized to ensure a consistent chemical composition. This is typically done in a pre-homogenization yard.
3. Raw Material Grinding
Ball Mill:
- The homogenized raw materials are fed into a ball mill. A ball mill is a type of grinder used to grind and blend materials for use in mineral dressing processes, paints, pyrotechnics, ceramics, and selective laser sintering.
Grinding Process:
- The ball mill consists of a hollow cylindrical shell rotating about its axis. The axis of the shell may be either horizontal or at a small angle to the horizontal. It is partially filled with balls made of steel, stainless steel, or rubber.
- The inner surface of the cylindrical shell is usually lined with an abrasion-resistant material such as manganese steel or rubber.
- The grinding media (balls) inside the ball mill are responsible for the grinding action. As the shell rotates, the balls are lifted up on the rising side of the shell and then they cascade down (or drop down on to the feed), from near the top of the shell. This action causes the balls to grind the raw materials into fine powder.
4. Homogenization of Raw Meal
- After grinding, the raw meal is stored in a homogenizing silo where it is mixed thoroughly to ensure a uniform composition.
5. Clinker Production
Kiln:
- The homogenized raw meal is then fed into a rotary kiln where it is heated to a high temperature (around 1450°C) to produce clinker. The kiln is a cylindrical vessel that rotates slowly about its axis.
Clinker Formation:
- Inside the kiln, the raw meal undergoes a series of chemical reactions to form clinker. The main reactions include the formation of calcium silicates and aluminates, which are the primary components of cement.
6. Clinker Grinding
Ball Mill:
- The clinker is then cooled and ground in another ball mill along with gypsum. The gypsum is added to control the setting time of the cement.
Final Grinding:
- The ball mill grinds the clinker and gypsum into a fine powder, which is the final product – cement.
7. Packaging and Storage
- The cement powder is then stored in silos before being packaged in bags or bulk for distribution.
Safety and Environmental Considerations
- Ensure that all safety protocols are followed during the entire process to prevent accidents.
- Implement dust control measures to minimize the release of cement dust into the environment.
- Properly dispose of any waste materials generated during the process.
By following these steps, you can produce cement powder using a ball mill. The process involves careful preparation of raw materials, precise grinding, and thorough mixing to ensure a high-quality final product.
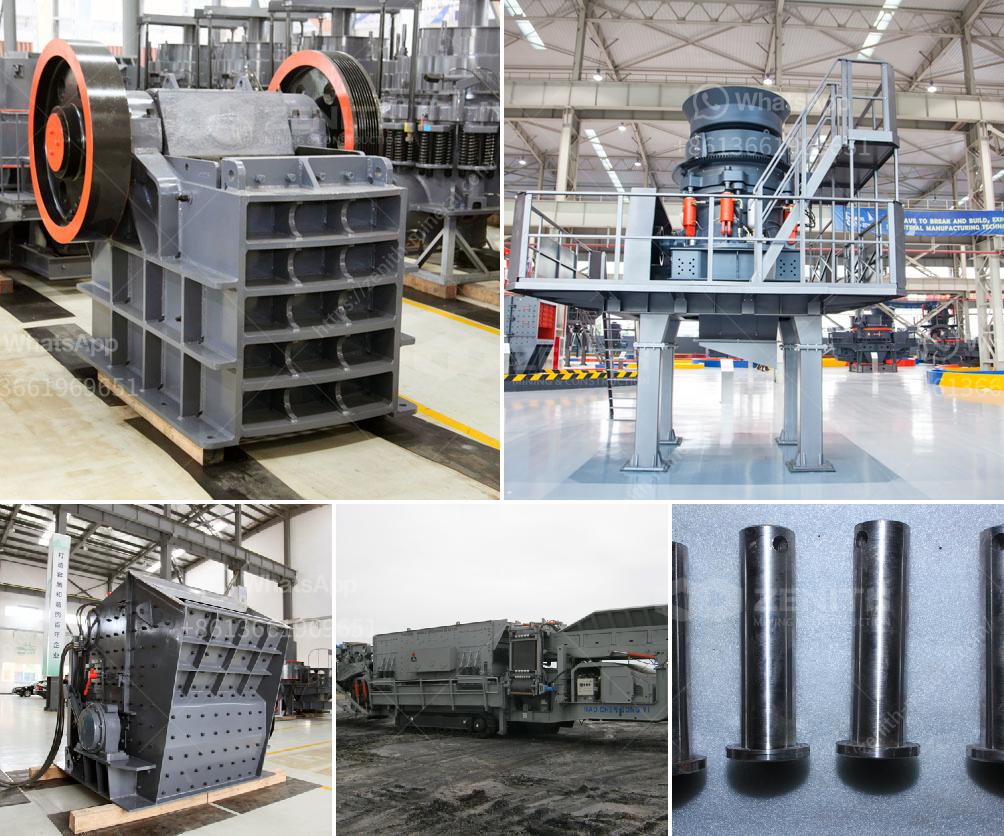