A line ball mill, often referred to as a ball mill for lined applications, operates on the principle of impact and attrition to grind materials into fine powders. Here’s a simplified overview of how it works:
-
Structure:
- Cylinder: A cylindrical shell that rotates around its axis.
- Lining: The interior surface can be lined with abrasion-resistant materials like rubber or manganese steel, which helps to protect the shell and enhance the mill's lifespan.
- Grinding Media: Steel balls, ceramic balls, or pebbles are placed inside the cylinder.
-
Operation:
- Loading: Raw materials and grinding media are loaded into the cylinder.
- Rotation: The cylinder is rotated by an external drive system. Rotation speed varies depending on the design and the desired fineness of the material.
- Motion: As the cylinder rotates, the motion causes the grinding media to lift and then cascade or tumble back down, crushing and grinding the material through impact and attrition.
-
Grinding Process:
- Impact: The balls drop from near the top of the shell and impact the material, breaking it down.
- Attrition: The continuous rotation causes repeated grinding, reducing the particle size progressively until the desired fineness is achieved.
-
Discharge:
- Depending on the design, the ground material is either discharged through an end grate or an air flow classifier, or it can leave the mill through a peripheral discharge.
-
Control and Efficiency:
- Speed: The speed of rotation can greatly affect the grinding efficiency and the final particle size.
- Load: The amount of material and grinding media must be optimized to ensure efficient grinding.
- Liner Design: The design and material of the liner can influence both the grinding efficiency and the wear rate of the mill.
Overall, a lined ball mill's efficiency and operational effectiveness depend on various factors, including the rotation speed, media size, material properties, and maintenance of the lining.
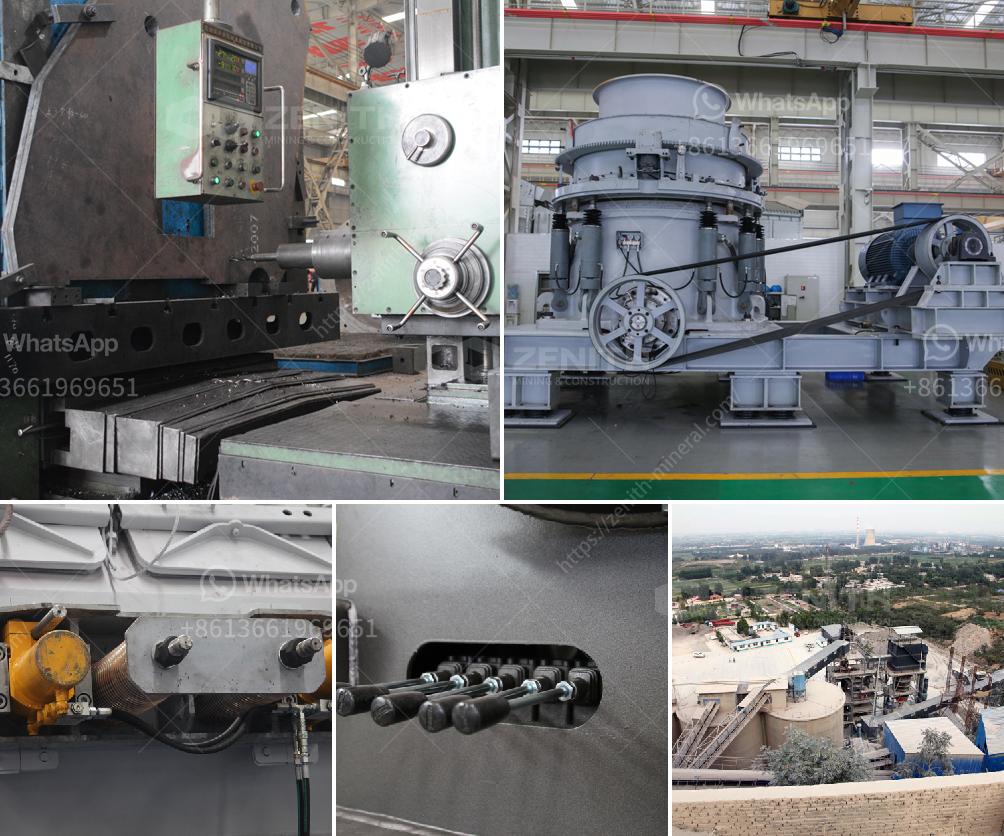