Extracting copper from tailings is a complex process that involves several steps to recover the valuable metal from waste material left after the initial extraction process. Here’s a general overview:
1. Sampling and Analysis
- Characterization: Perform a detailed analysis to determine the copper content and composition of the tailings.
- Testing: Conduct laboratory tests to find the most effective extraction method for the specific type of tailings.
2. Crushing and Grinding
- Size Reduction: Crush and grind the tailings to liberate the copper minerals from the surrounding material. This increases the surface area for the extraction process.
3. Concentration Techniques
- Froth Flotation: This is the most common method for copper extraction, where crushed ore is mixed with water and chemicals to create a slurry. Air is then bubbled through the mixture, causing the copper-containing minerals to attach to the bubbles and float to the surface, forming a froth that can be skimmed off.
- Gravity Separation: Sometimes used if the copper minerals are heavier than the tailings.
4. Leaching
- Acid Leaching: Tailings can be treated with sulfuric acid to dissolve the copper. The solution containing the dissolved copper is then collected.
- Bioleaching: Involves using bacteria to leach copper from the tailings. This method is slower but can be more environmentally friendly.
5. Solvent Extraction and Electrowinning (SX/EW)
- Solvent Extraction: The copper-laden solution is mixed with an organic solvent that selectively binds to copper ions.
- Electrowinning: The copper-rich organic solution is then subjected to electrical current to deposit pure copper onto cathodes through an electrochemical process.
6. Environmental and Regulatory Considerations
- Tailings Management: Ensure responsible disposal or storage of tailings to minimize environmental impact.
- Regulatory Compliance: Follow all local and international regulations related to mining and waste management.
7. Optimization and Recovery
- Continuous Monitoring: Track the efficiency and recovery rates of the extraction process.
- Process Optimization: Adjust and fine-tune the process to maximize copper extraction and reduce operational costs.
Equipment Needed
- Crushers and Grinders: For initial size reduction.
- Flotation Cells: For froth flotation.
- Leaching Tanks: For acid or bioleaching.
- Solvent Extraction Units: For separating copper from the leach solution.
- Electrowinning Equipment: For the final copper recovery stage.
Safety and Sustainability
- Personal Protective Equipment (PPE): Ensure workers are equipped with necessary safety gear.
- Sustainable Practices: Implement practices to minimize environmental impact, such as recycling water and reusing chemicals where possible.
By following these steps and continuously seeking ways to improve the process, copper can be effectively extracted from tailings, making what was once waste into a valuable resource.
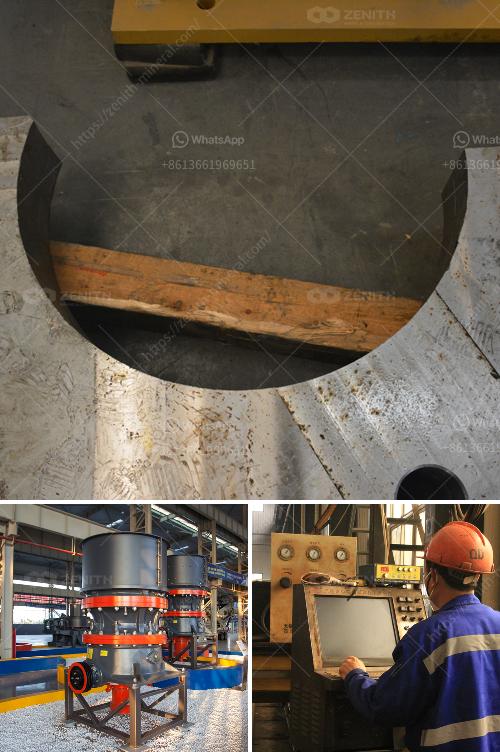