Sure, here’s a detailed plan for a 150 TPH (tons per hour) hematite ore crushing plant:
Introduction
A 150 TPH hematite ore crushing plant is meant to crush and process the hematite ore for various industrial purposes. This includes extraction of iron for steel manufacturing.
Plant Components
-
Feed Hopper:
- Function: Receives and stores raw hematite ore.
- Capacity: Designed to hold a few hours worth of ore to ensure continuous operation.
-
Primary Crusher (Jaw Crusher):
- Function: Initial size reduction of the raw ore.
- Capacity: 150 TPH.
- Output Size: 50-100mm, depending on the crusher settings.
-
Conveyor Belts:
- Function: Transporting material between different sections of the plant.
- Belt Width and Speed: Designed according to the plant capacity.
-
Secondary Crusher (Cone Crusher)
- Function: Further reduces the ore size.
- Capacity: 150 TPH.
- Output Size: 25-50mm, adjustable settings.
-
Vibrating Screens:
- Function: Separate crushed ore into multiple size categories.
- Capacity and Specifications: Double or triple-deck screens to handle 150 TPH.
-
Tertiary Crusher (Impact Crusher)
- Function: Final size reduction to meet specific size requirements.
- Capacity: 150 TPH.
- Output Size: 5-20mm, customizable settings.
-
Screening Equipment:
- Function: Final product separation and size classification.
- Capacity: Capable of processing all the ore throughput from crushers.
-
Product Silos/Storage:
- Function: Store the final product before dispatch.
- Capacity: Sized to store a full day’s worth of output to manage logistics efficiently.
Additional Systems
-
Dust Collection System:
- Ensures environmental compliance by managing dust generated during crushing and conveying.
-
Control System:
- Centralized control unit for monitoring and managing the entire plant's operations.
- PLC/SCADA systems for automated operation and real-time monitoring.
-
Water Supply System:
- For dust suppression and cooling systems within crushers to maintain optimal operation temperature.
Layout Considerations
- Accessibility: Ensure plant layout allows easy access to all components for maintenance and operation.
- Safety: Adequate safety measures including emergency stops, safety rails, and signage.
- Space: Allow sufficient space for potential future expansion and easy transportation of machinery.
Operational Workflow
- Raw hematite ore is delivered to the feed hopper.
- Primary crushing in the jaw crusher.
- Conveyed to secondary crushing via conveyor belts.
- Secondary crushing in the cone crusher.
- Material screened for size classification.
- Oversized material is sent to the tertiary crusher.
- Final size classification and storage.
Conclusion
Efficiently managing a 150 TPH hematite ore crushing plant requires careful planning and coordination of various components. Ensuring the proper selection and maintenance of equipment will result in a high-quality end product and a successful operation.
Feel free to ask any additional details or clarify specific parts of the plant setup!
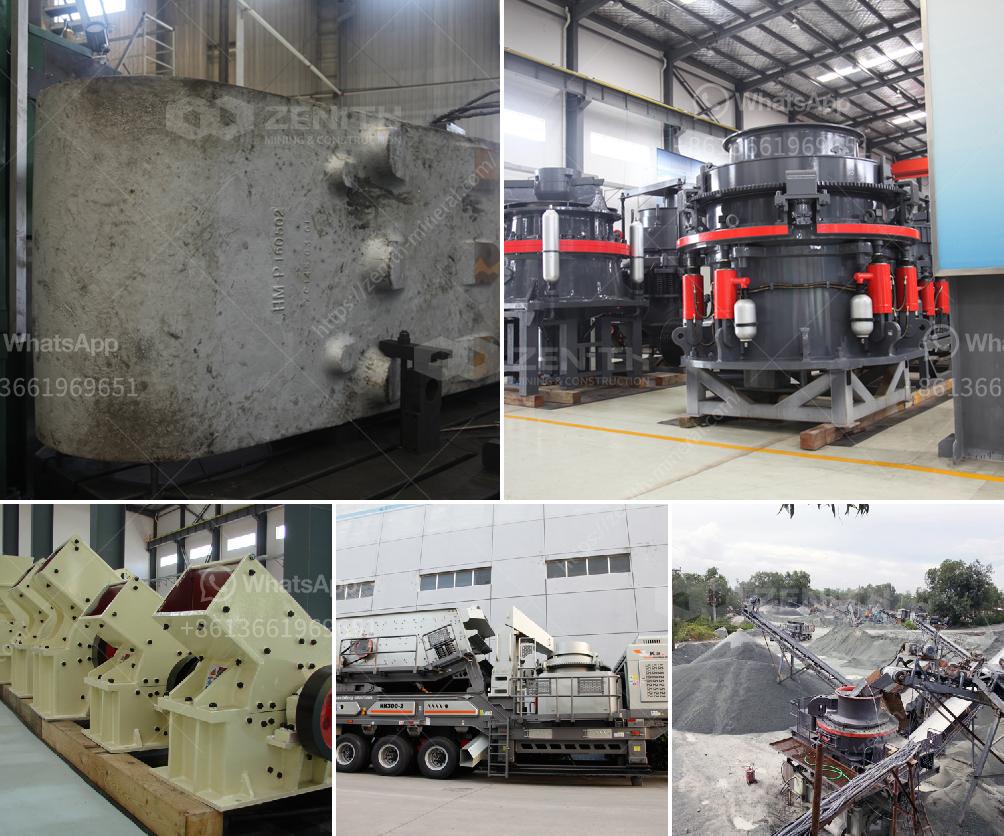