To create a detailed and comprehensive response regarding a "20tph ferrochrome slag recovery plant," let's break down the various aspects involved in such a project. This will include an overview of ferrochrome slag, the recovery process, the equipment used, and the potential benefits and challenges.
Overview of Ferrochrome Slag
Ferrochrome slag is a byproduct of the production of ferrochrome, an alloy of chromium and iron, which is used in the production of stainless steel and other alloys. The slag is generated during the smelting process when impurities are separated from the molten metal. This slag contains valuable metals and minerals that can be recovered and reused, making the recovery process both economically and environmentally beneficial.
Recovery Process
The recovery process for ferrochrome slag typically involves several stages, including:
- Crushing and Grinding: The slag is first crushed and ground to liberate the metal particles from the non-metallic components.
- Screening: The ground material is then screened to separate particles of different sizes.
- Magnetic Separation: Magnetic separators are used to remove ferromagnetic materials from the slag.
- Gravity Separation: Gravity separation techniques, such as jigs, spirals, or shaking tables, are used to separate heavier metal particles from lighter non-metallic particles.
- Flotation: In some cases, flotation techniques may be used to further concentrate the metal particles.
- Smelting: The recovered metal particles can be smelted to produce ferrochrome or other valuable alloys.
Equipment Used
A 20tph (tons per hour) ferrochrome slag recovery plant would typically include the following equipment:
- Jaw Crusher: For primary crushing of the slag.
- Ball Mill or Rod Mill: For grinding the crushed slag.
- Vibrating Screen: For screening the ground material.
- Magnetic Separator: For removing ferromagnetic materials.
- Gravity Separator: Such as jigs, spirals, or shaking tables for separating metal particles.
- Flotation Cells: For further concentration of metal particles (if needed).
- Smelting Furnace: For smelting the recovered metal particles.
Benefits
The recovery of ferrochrome slag offers several benefits:
- Economic Value: Recovering valuable metals from slag can generate additional revenue.
- Resource Efficiency: It allows for the reuse of materials that would otherwise be considered waste.
- Environmental Impact: Reduces the environmental footprint by minimizing waste and reducing the need for mining new raw materials.
- Energy Savings: Recycling metals typically requires less energy than producing them from raw ores.
Challenges
Despite the benefits, there are also challenges associated with ferrochrome slag recovery:
- Complexity of the Process: The recovery process involves multiple stages and requires specialized equipment and expertise.
- Quality of the Slag: The composition of the slag can vary, affecting the efficiency of the recovery process.
- Initial Investment: Setting up a recovery plant requires significant capital investment.
- Regulatory Compliance: Ensuring compliance with environmental and safety regulations can be challenging.
Conclusion
A 20tph ferrochrome slag recovery plant involves a complex process that includes crushing, grinding, screening, magnetic and gravity separation, and possibly flotation and smelting. The plant requires specialized equipment and expertise but offers significant economic and environmental benefits. However, challenges such as process complexity, slag quality, initial investment, and regulatory compliance must be addressed to ensure successful operation.
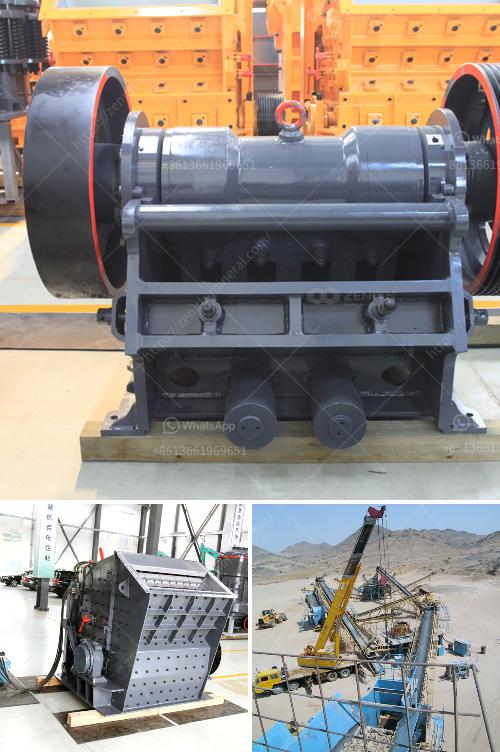