Sure, let's break down the requirements for a "20tph tantalum niobium mining plant" and provide a detailed explanation of what such a plant might involve.
Overview
A "20tph tantalum niobium mining plant" refers to a facility designed to process 20 tons per hour (tph) of ore containing tantalum and niobium. Tantalum and niobium are rare, valuable metals used in various high-tech applications, including electronics, aerospace, and medical devices. The mining plant's primary goal is to extract these metals efficiently and economically.
Key Components and Processes
-
Ore Extraction:
- Mining: The first step involves extracting the ore from the earth. This can be done through open-pit mining or underground mining, depending on the location and depth of the ore body.
- Transport: Once the ore is extracted, it needs to be transported to the processing plant. This can be done using trucks, conveyors, or other transportation methods.
-
Crushing and Grinding:
- Primary Crushing: The ore is initially crushed to reduce its size. This is typically done using jaw crushers or gyratory crushers.
- Secondary Crushing: Further size reduction is achieved using cone crushers or impact crushers.
- Grinding: The crushed ore is then ground to a fine powder using ball mills or rod mills. This increases the surface area for the subsequent processing steps.
-
Concentration:
- Gravity Separation: Tantalum and niobium minerals are often heavier than the surrounding gangue minerals. Gravity separation methods, such as shaking tables, spirals, and jigs, can be used to concentrate the valuable minerals.
- Magnetic Separation: Some tantalum and niobium minerals are magnetic. Magnetic separators can be used to separate these minerals from non-magnetic gangue.
- Flotation: In some cases, flotation methods can be used to concentrate the tantalum and niobium minerals. This involves adding chemicals to the slurry to make the valuable minerals hydrophobic, allowing them to be separated from the gangue.
-
Leaching and Solvent Extraction:
- Leaching: The concentrated ore may be subjected to leaching, where chemicals are used to dissolve the tantalum and niobium. This is often done using hydrofluoric acid or other strong acids.
- Solvent Extraction: The dissolved metals are then separated from the leach solution using solvent extraction techniques. This involves mixing the solution with an organic solvent that selectively extracts the tantalum and niobium.
-
Purification and Refining:
- Precipitation: The extracted metals are precipitated from the solution, often by adding a reducing agent or changing the pH.
- Calcination: The precipitated metals are then heated to high temperatures to remove any remaining impurities and convert them to their oxide forms.
- Reduction: The metal oxides are reduced to their metallic forms using reducing agents such as hydrogen or carbon.
-
Final Product Handling:
- Melting and Casting: The purified metals are melted and cast into ingots or other desired shapes.
- Quality Control: The final products are subjected to rigorous quality control tests to ensure they meet the required specifications.
Environmental and Safety Considerations
- Waste Management: Proper disposal of tailings and other waste materials is crucial to minimize environmental impact. Tailings dams and other containment methods are often used.
- Water Management: Mining and processing operations require significant amounts of water. Recycling and treating water to reduce consumption and prevent contamination is essential.
- Safety Protocols: Ensuring the safety of workers is paramount. This includes providing proper training, protective equipment, and implementing safety protocols to prevent accidents.
Economic and Logistical Factors
- Cost Analysis: A detailed cost analysis is necessary to determine the feasibility of the mining operation. This includes capital costs, operating costs, and potential revenue from the sale of tantalum and niobium.
- Supply Chain Management: Efficient supply chain management is crucial to ensure a steady supply of raw materials and the timely delivery of final products to customers.
- Regulatory Compliance: Adhering to local and international regulations is essential to avoid legal issues and ensure sustainable operations.
Conclusion
A 20tph tantalum niobium mining plant involves a complex series of processes and components designed to extract and refine these valuable metals. From ore extraction to final product handling, each step requires careful planning and execution to ensure efficiency, safety, and environmental sustainability. By understanding the intricacies of each stage, operators can optimize their operations and maximize the economic benefits of their mining activities.
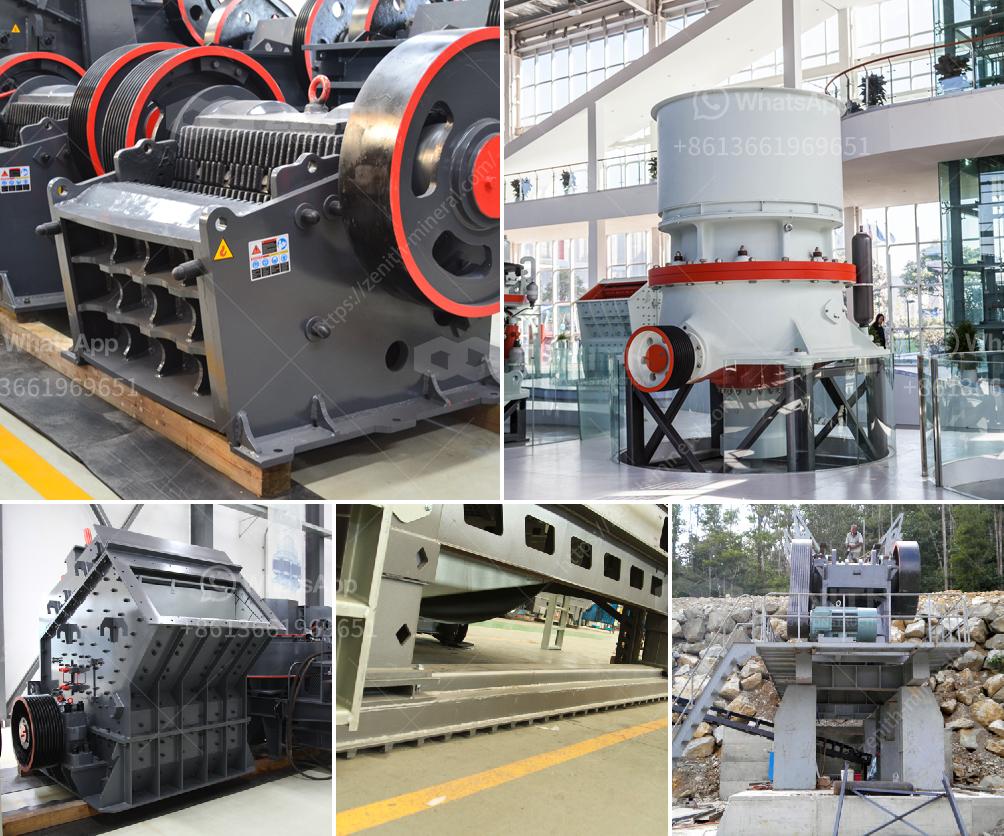