A 20 TPH (tons per hour) tungsten ore processing plant includes several crucial components to manage and process the ore effectively. Here's a breakdown of what such a plant might involve:
1. Crushing and Grinding
- Primary Crusher: Jaw crusher to reduce the size of the mined tungsten ore.
- Secondary Crusher: Cone crusher or impact crusher for further size reduction.
- Grinding Mill: Ball mill or rod mill to fine-tune the ore particles.
2. Screening and Classification
- Vibrating Screens: To segregate materials by particle size.
- Spiral Classifiers or Cyclones: To separate particles based on size and density.
3. Concentration and Separation
- Gravity Separation: Equipment like shaking tables, spirals, or jigs to separate tungsten from other materials based on density.
- Flotation Cells: To further refine the tungsten concentrate.
4. Thickening and Dewatering
- Thickener Tanks: To concentrate the slurry and reduce water content.
- Filter Presses or Vacuum Filters: To dewater the concentrate.
5. Material Handling
- Conveyors and Feeders: To transport materials between different stages.
- Slurry Pumps: To handle the transport of slurry between processing units.
6. Auxiliary Systems
- Water Management System: For recycling and managing process water.
- Dust Collection System: To manage dust generated during crushing and grinding.
- Electrical and Control Systems: To automate and control the plant's processes.
Key Considerations
- Ore Characteristics: The plant design should account for the specific characteristics of the tungsten ore, such as hardness and mineral composition.
- Environmental Regulations: Compliance with local environmental laws regarding emissions, waste management, and water usage.
- Economic Efficiency: Ensure that the plant operates cost-effectively while achieving a high recovery rate of tungsten.
Typical Workflow
- Ore Reception: Raw tungsten ore is fed into the primary crusher.
- Crushing: The ore is crushed to a smaller size.
- Grinding: Further size reduction to achieve fine powders.
- Concentration: Separation of tungsten from the gangue minerals.
- Thickening & Dewatering: Reducing the water content of the final concentrate.
- Final Product: Purified tungsten ready for refining or sale.
For more detailed design and engineering, consultation with experts in mineral processing and automation technologies will be essential.
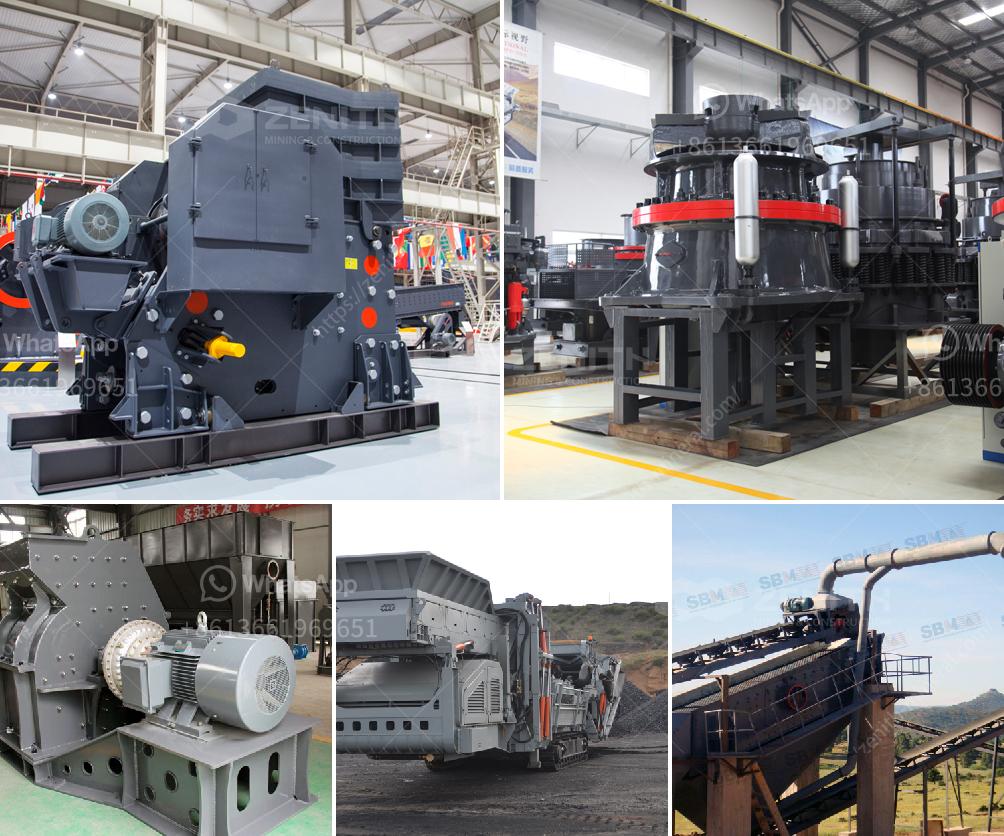