To design a 240 tons per hour (tph) iron ore processing plant, several key components and processes need to be considered. Below is a detailed breakdown of the essential elements and steps involved in setting up such a plant:
1. Ore Reception and Storage
- Ore Reception: The raw iron ore is received from the mine and transported to the plant via trucks or conveyors.
- Storage: The ore is stored in stockpiles or silos to ensure a consistent feed to the processing plant.
2. Crushing and Screening
- Primary Crushing: The ore is initially crushed to reduce its size. This is typically done using a jaw crusher.
- Secondary Crushing: Further size reduction is achieved using cone crushers or impact crushers.
- Screening: The crushed ore is screened to separate fine particles from coarse particles. Screens with different mesh sizes are used to achieve the desired size distribution.
3. Grinding
- Primary Grinding: The coarse ore is ground in a primary grinding mill, such as a ball mill or a rod mill, to further reduce its size.
- Secondary Grinding: The ore is then ground in a secondary mill to achieve the required particle size for the next stage of processing.
4. Classification
- Hydrocyclones: The ground ore is classified using hydrocyclones to separate fine particles from coarse particles.
- Spiral Classifiers: Alternatively, spiral classifiers can be used for classification.
5. Concentration
- Magnetic Separation: Magnetic separators are used to separate magnetic iron ore from non-magnetic impurities.
- Gravity Separation: Gravity separation methods, such as jigs, spirals, and shaking tables, are used to concentrate the ore based on density differences.
- Flotation: In some cases, flotation is used to separate valuable minerals from the ore.
6. Thickening and Filtration
- Thickening: The concentrated ore slurry is thickened using thickeners to remove excess water.
- Filtration: The thickened slurry is filtered to produce a dry concentrate.
7. Tailings Management
- Tailings Disposal: The waste material (tailings) from the processing plant is managed and disposed of in tailings ponds or dry stacks.
- Water Recycling: Water used in the processing plant is recycled to minimize water consumption and reduce environmental impact.
8. Product Handling and Storage
- Concentrate Storage: The final iron ore concentrate is stored in silos or stockpiles before being transported to the customer.
- Loading and Transportation: The concentrate is loaded onto trucks, trains, or ships for transportation to the end user.
9. Control and Automation
- Process Control: The entire processing plant is monitored and controlled using a centralized control system to ensure optimal performance and efficiency.
- Automation: Advanced automation systems are used to control various processes, reduce manual intervention, and improve safety.
10. Environmental and Safety Considerations
- Dust Control: Dust suppression systems are installed to minimize dust emissions during ore handling and processing.
- Noise Control: Noise reduction measures are implemented to protect workers and the surrounding community.
- Safety Measures: Safety protocols and equipment are in place to protect workers from potential hazards.
11. Utilities and Infrastructure
- Power Supply: A reliable power supply is essential for the operation of the processing plant.
- Water Supply: Adequate water supply is required for various processes, including grinding, classification, and concentration.
- Infrastructure: Supporting infrastructure, such as roads, buildings, and communication systems, is necessary for the smooth operation of the plant.
Conclusion
Designing and setting up a 240 tph iron ore processing plant involves careful planning and consideration of various components and processes. Each stage of the process, from ore reception to product handling, plays a crucial role in ensuring the efficient and effective processing of iron ore. By implementing advanced technologies and adhering to environmental and safety standards, the plant can achieve optimal performance and sustainability.
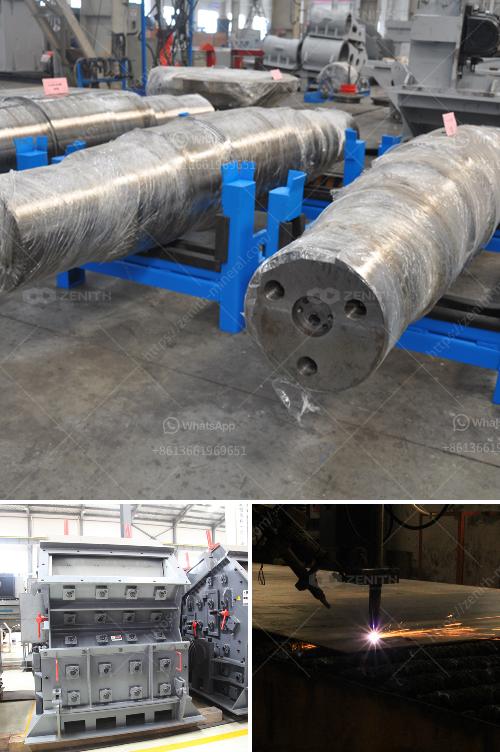