It seems like you are referring to a "250tph coal washing plant." This type of plant is designed to process coal at a rate of 250 tons per hour (tph). Coal washing, also known as coal preparation or coal beneficiation, is a process that removes impurities from raw coal to improve its quality and make it suitable for specific applications.
Key Components and Processes in a 250tph Coal Washing Plant
-
Raw Coal Handling:
- Feed Hopper: The raw coal is initially fed into a hopper, which regulates the flow of coal into the washing plant.
- Conveyor Belts: These transport the coal from the hopper to various processing units within the plant.
-
Screening:
- Vibrating Screens: These are used to separate coal particles based on size. The screens can have different mesh sizes to classify coal into various size fractions.
-
Crushing:
- Crushers: These reduce the size of larger coal lumps to a manageable size for further processing. Common types include jaw crushers, cone crushers, and impact crushers.
-
Washing and Separation:
- Dense Medium Cyclones (DMC): These use a dense medium (usually a mixture of water and magnetite) to separate coal from impurities based on density differences.
- Jigs: These are gravity separation devices that use pulsating water to stratify coal and impurities.
- Spirals: These use centrifugal force to separate coal particles based on density and size.
-
Dewatering:
- Centrifuges: These remove excess water from the washed coal.
- Thickeners: These concentrate the slurry by removing water, producing a thickened underflow and a clarified overflow.
- Drying Screens: These further reduce the moisture content of the coal.
-
Tailings Management:
- Tailings Ponds: These are used to store and manage the waste material (tailings) generated during the washing process.
- Filter Presses: These dewater the tailings to reduce the volume of waste and recover water for reuse in the plant.
-
Control Systems:
- SCADA (Supervisory Control and Data Acquisition): This system monitors and controls the various processes within the plant, ensuring efficient and safe operation.
Benefits of Coal Washing
- Improved Quality: Washing removes impurities such as ash, sulfur, and other contaminants, resulting in higher-quality coal.
- Increased Efficiency: Clean coal burns more efficiently, leading to better performance in power plants and industrial applications.
- Environmental Benefits: Reduced emissions of pollutants such as sulfur dioxide (SO2) and particulate matter (PM) due to the removal of impurities.
- Economic Advantages: Higher-quality coal can command a better price in the market, and improved efficiency can reduce operational costs.
Challenges and Considerations
- Water Usage: Coal washing requires significant amounts of water, which can be a challenge in areas with limited water resources.
- Waste Management: Proper disposal and management of tailings and other waste materials are crucial to minimize environmental impact.
- Energy Consumption: The washing process itself consumes energy, which needs to be balanced against the benefits of improved coal quality.
In summary, a 250tph coal washing plant is a complex facility designed to improve the quality of coal by removing impurities. It involves various processes and equipment, each playing a crucial role in ensuring the efficient and effective washing of coal. The benefits of coal washing include improved quality, increased efficiency, and environmental advantages, but it also comes with challenges such as water usage and waste management.
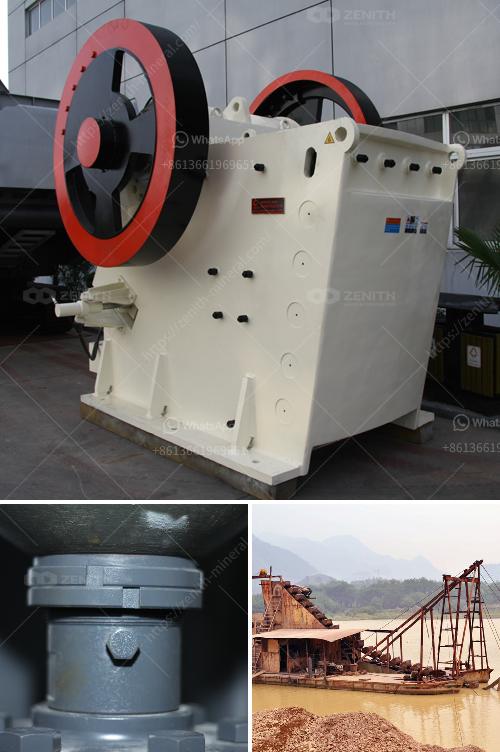