Creating a 5 tons per hour (tph) rock tin processing plant involves several key stages and equipment for optimal recovery of tin from the ore. Below is a basic outline of the essential steps and machinery required:
1. Crushing and Grinding
Crushing:
- Jaw Crusher: For primary crushing to reduce the size of ore from large rocks to smaller manageable pieces.
- Cone Crusher or Hammer Crusher: For secondary crushing to achieve finer particle sizes.
Grinding:
- Ball Mill or Rod Mill: To further grind the ore to liberate tin particles from the rock matrix. This is essential for the subsequent concentration steps.
2. Screening
- Vibrating Screen: To classify crushed ore into various particle sizes for effective processing in downstream operations.
3. Gravity Separation
- Spiral Chute: For the initial concentration by taking advantage of the different specific gravities of tin and gangue materials.
- Shaking Table: To further concentrate the tin ore by separating it from lighter gangue material.
4. Magnetic Separation
- Magnetic Separator: This step helps in removing any iron impurities from the concentrate, if present.
5. Flotation (Optional)
- Flotation Cells: If the ore contains sulfides (like cassiterite), flotation can be used to separate these from the tin.
6. Dewatering
- Thickener: To concentrate the slurry before drying.
- Filter Press: To remove remaining moisture from the concentrate.
7. Auxiliary Equipment
- Pumps and Piping: For slurry transport between different stages.
- Conveyor Belts: For the transport of material between crushers, screens, and other equipment.
- Water Treatment System: To recycle water used in the processing plant and ensure environmental compliance.
Implementation Steps:
- Ore Assessment: Evaluation of the ore characteristics to design the most efficient processing route.
- Plant Design & Layout: Create a detailed layout of the processing plant, ensuring optimal flow of materials and ease of maintenance.
- Construction & Installation: Build infrastructure and install the selected equipment.
- Commissioning: Test and adjust the processing plant to ensure it operates as designed.
- Operation & Maintenance: Continuous operation of the plant with regular maintenance to ensure maximum efficiency and longevity of the equipment.
Conclusion:
Establishing a 5tph rock tin processing plant requires careful planning and selection of suitable equipment. The combination of crushing, grinding, gravity separation, and auxiliary systems ensures the effective recovery of tin ore. Regular monitoring and maintenance will help to achieve consistent performance and optimal production.
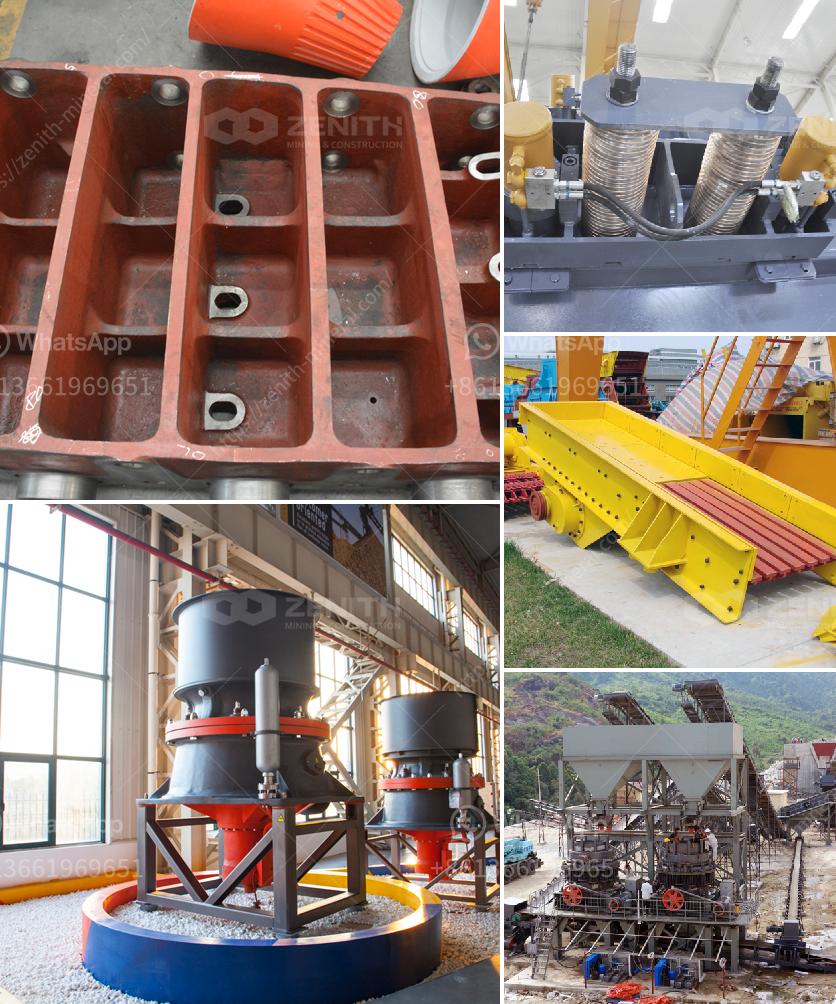