A 5 tons per hour (tph) rock tungsten processing plant typically involves several stages to efficiently extract tungsten from ore. Here’s an overview of what such a plant might include:
-
Crushing Stage:
- Jaw Crusher: Used to crush the raw ore into smaller pieces, often down to 20-50mm.
- Cone Crusher: Further reduces the size of ore particles.
-
Grinding Stage:
- Ball Mill or Rod Mill: Grinds the crushed ore into fine particles, preparing it for separation processes.
-
Gravity Separation Stage:
- Jig Separator: Separates particles based on their specific gravity, concentrating the tungsten ore.
- Shaking Table: Further refines the ore, ensuring a higher concentration of tungsten.
-
Flotation Stage (optional):
- Flotation Machine: Removes impurities from the tungsten concentrate, enhancing purity levels if required.
-
Magnetic Separation (if applicable):
- Magnetic Separator: Removes magnetic minerals from the tungsten concentrate, improving the quality of the final product.
-
Dewatering:
- Thickener: Concentrates the ore slurry by removing excess water.
- Filter Press: Further reduces moisture content in the concentrate.
-
Final Product Handling:
- Dryer: Dries the concentrated tungsten ore.
- Packaging: Prepares the final product for shipment or further processing.
These stages are integral to the efficient processing of tungsten ore. The plant design would also include essential infrastructure such as storage facilities, water supply systems, and waste management solutions to ensure smooth operation.
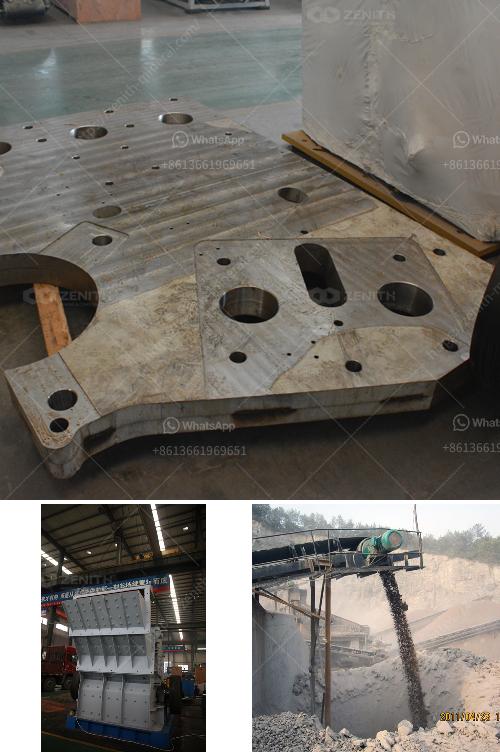