Certainly! Here's an overview of an 80 tons per hour (tph) granite crushing process:
1. Initial Considerations
- Material: Granite
- Capacity: 80 tph
- Final Product Size: Desired particle size for the final product
- Location: Site logistics and environmental considerations
2. Primary Crushing
- Equipment: Jaw Crusher or Gyratory Crusher
- Purpose: To reduce large granite boulders (up to 1 meter in diameter) to smaller chunks, usually around 20-30 cm in size.
- Configuration: This depends on the natural granularity of the granite at the site, but typically involves a primary jaw crusher.
3. Secondary Crushing
- Equipment: Cone Crusher or Impact Crusher
- Purpose: To further reduce the size of the granite pieces from the primary crusher, achieving a size of about 5-10 cm.
4. Screening
- Equipment: Vibrating Screen or Grizzly Screen
- Purpose: To sort the crushed material into different size ranges.
- Process: Separated into various grades, with unqualified sizes being recirculated back into the crushers.
5. Tertiary Crushing
- Equipment: Cone Crusher or Sand Making Machine
- Purpose: To achieve the final desired product size, often down to sand-like granules or specific aggregate sizes needed for construction purposes.
6. Material Handling
- Components: Conveyors, Feeders, Vibrating Grizzly, Hopper
- Purpose: To effectively move material through the various stages and ensure a continuous feed to crushers and screens.
7. Dust and Noise Control (Optional)
- Equipment: Dust suppression systems, Noise barriers
- Purpose: To maintain environmental standards and reduce the impact on surrounding areas.
8. Control Systems
- Automation: Ensure consistent throughput and efficient operation
- SCADA/PLC Control: For real-time monitoring and adjustments
9. Quality Control
- Lab Testing: Ensuring the final product meets specific quality standards
- Routine Checks: Regularly checking equipment for wear and tear
Example Workflow:
- Feeding: Granite boulders are fed into the jaw crusher through the vibrating feeder.
- Primary Crushing: The large granite blocks are reduced to a manageable size.
- Secondary Crushing: Material from the primary crusher is fed into the cone crusher.
- Screening: Crushed granite is separated into various sizes; oversized material is recirculated.
- Tertiary Crushing: Final crushing stage to get the desired size (if necessary).
- Stockpiling: Aggregates are stored for transport or further processing.
End Products:
- Gravel, aggregate, sand, or specific granite products for construction projects.
Safety and Maintenance
- Regular inspections and safety checks.
- Scheduled maintenance to avoid breakdowns and ensure consistent performance.
By following these steps, you can effectively process granite at an 80tph capacity, yielding high-quality, consistent products for various construction and industrial applications.
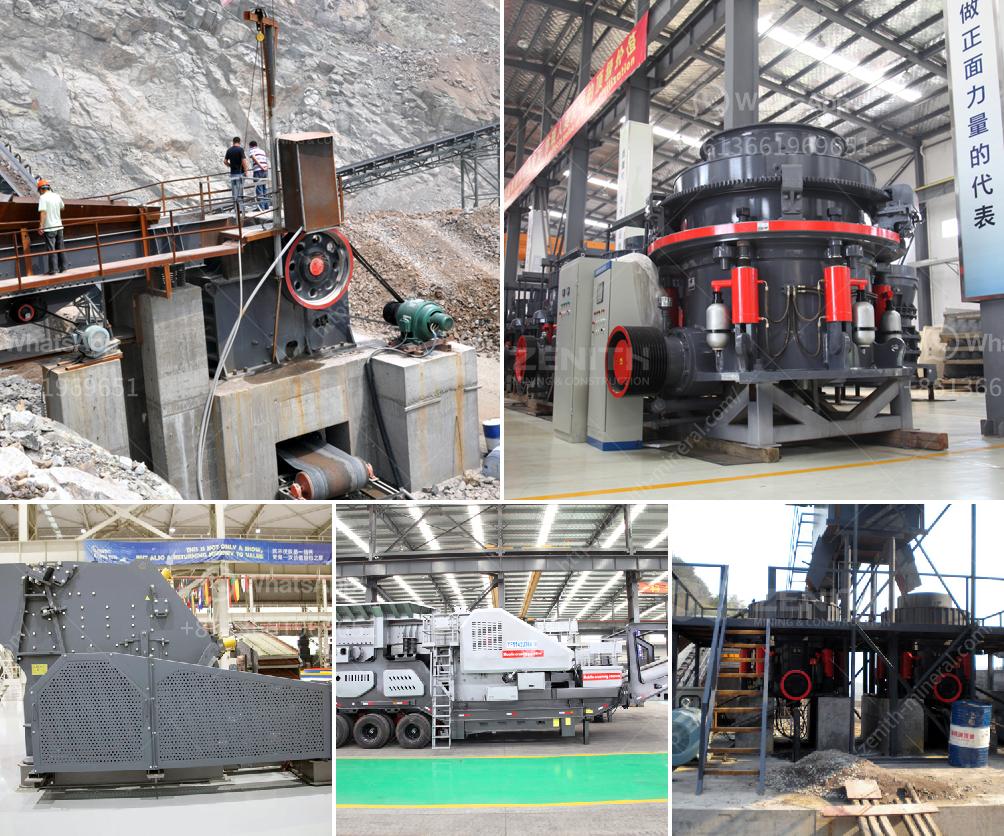