Certainly! Here’s an overview of a case study on an 8 tonnes per hour (8TPH) diamond mining process flow in Angola.
Case Study: 8TPH Diamond Mining Process Flow in Angola
Introduction:
Angola is renowned for its rich diamond deposits, making diamond mining a significant part of its economy. This case study focuses on an artisanal mining operation designed to process 8 tonnes of ore per hour to efficiently extract diamonds.
Objective:
To outline the diamond extraction process flow for an 8TPH diamond mining operation in Angola, ensuring high recovery rates while maintaining cost-efficiency and environmental sustainability.
Process Flow:
-
Ore Extraction:
- The mining process begins with the extraction of ore from the alluvial or kimberlite deposits using excavation and mechanical methods such as hydraulic shovels and excavators.
-
Primary Crushing:
- Extracted ore is transported to a primary crusher to reduce large rocks into smaller, manageable sizes, typically under 30 mm in diameter.
-
Feeding:
- The crushed ore is then fed into a vibrating feeder that distributes the material evenly to the subsequent processing stages.
-
Scrubbing and Screening:
- Scrubbing: The ore material undergoes scrubbing to remove clay and other soluble materials using rotary scrubbers or trommels.
- Screening: Post-scrubbing, the material is passed through vibrating screens to separate particles by size. Oversized particles are recirculated back to the crusher.
-
Dense Media Separation (DMS):
- The screened material enters the Dense Media Separation process where it is mixed with a ferrosilicon-based dense medium. The separation relies on the specific gravity difference between diamonds and the waste material.
- Diamonds, having higher specific gravity, sink and are collected, while the lighter waste material floats and is discarded.
-
Concentration:
- The diamond-rich concentrate is then subjected to additional concentration processes. These may include jigging and spiral separators to further purify the diamond concentrate from remaining impurities.
-
Recovery:
- X-Ray Fluorescence (XRF): The concentrated material is passed through XRF machines which detect and separate diamonds based on their fluorescence properties.
- Final Sorting: Manual sorting and further refining are carried out to achieve the final high-purity diamond product ready for market.
-
Tailings Management:
- Tailings, or the waste material remaining after diamond extraction, are responsibly managed. Methods such as thickening, filtration, and secure deposition are employed to minimize environmental impact.
Conclusion:
The 8TPH diamond mining operation in Angola highlights an efficient and effective process flow encompassing extraction, crushing, scrubbing, dense media separation, concentration, and final recovery. Sustainable tailings management is a critical component, ensuring minimal environmental impact. This standardized approach ensures high diamond recovery rates and operational cost-efficiency, contributing to Angola's economic growth while promoting responsible mining practices.
Key Takeaways:
- Efficient diamond extraction is achieved through a well-integrated process flow.
- Proper scrubbing and screening are essential for removing unwanted materials.
- Dense media separation is pivotal in isolating diamonds from ore.
- Advanced technologies like XRF enhance diamond recovery and purity.
- Responsible tailings management promotes environmental sustainability.
By following this detailed process flow, diamond mining operations in Angola can achieve optimal results in terms of both diamond recovery and environmental responsibility.
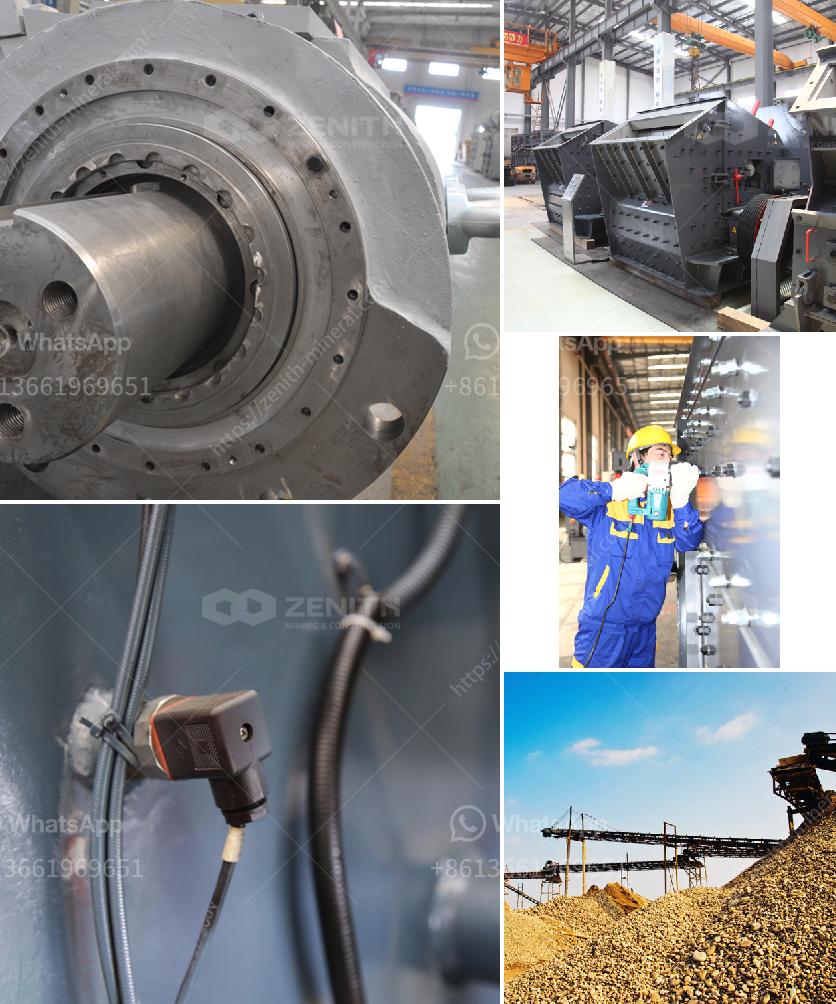