An 8 Tons Per Hour (TPH) kaolin process plant typically involves several key stages to efficiently process kaolin clay and produce high-quality final products. Here’s an overview of what such a plant might include:
-
Raw Material Handling:
- Feed Hopper: Where raw kaolin clay is initially dumped.
- Conveyor Belts: Transporting the raw material to different processing stages.
-
Crushing and Grinding:
- Jaw Crusher: For primary crushing to reduce large chunks of kaolin into smaller pieces.
- Milling Equipment: Such as ball mills or hammer mills to further reduce the particle size.
-
Screening and Separation:
- Vibratory Screens: To separate particles based on size.
- Hydrocyclones: For further separation and classification based on density and size.
-
Degritting:
- Attrition Scrubbers: To remove coarse particles and grit.
-
Beneficiation and Washing:
- Thickeners: To concentrate the kaolin slurry and remove impurities.
- Flotation Cells: To separate kaolin from other minerals.
- Water Washing: For additional purification and brightness enhancement.
-
Drying:
- Spray Dryers or Rotary Dryers: To remove moisture content from the kaolin.
-
Calcination:
- Rotary Kilns: For heating kaolin to high temperatures to achieve desired properties.
-
Air Classification:
- To segregate fine particles and achieve uniformity in product size.
-
Packing and Storage:
- Silos, Bagging Units: For storing and packaging the final product for shipment.
-
Quality Control:
- Laboratory Testing: To ensure the product meets industry standards and specifications.
Each of these stages can be tailored to the specific requirements of the plant and the properties of the raw kaolin being processed. Having an efficient and well-designed plant helps ensure consistent product quality, minimal environmental impact, and cost effectiveness.
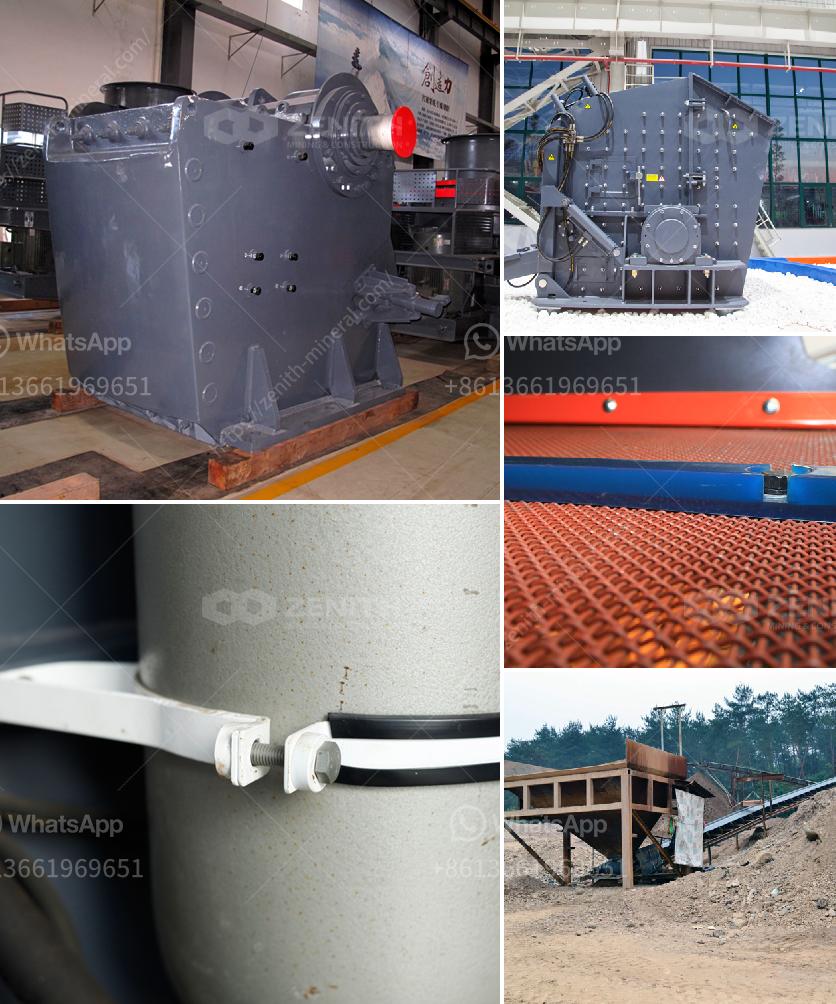