The process of mining iron ore involves several stages, each of which is crucial to the successful extraction and processing of the ore. Here is a detailed breakdown of the entire process:
-
Exploration and Prospecting:
- Geological Surveys: The first step in mining iron ore is to conduct geological surveys to identify areas with potential iron ore deposits. This involves studying the geological formations and using various techniques such as aerial surveys, satellite imagery, and geophysical methods.
- Sampling and Drilling: Once a potential site is identified, samples are collected through drilling. These samples are analyzed to determine the quality and quantity of the iron ore present.
-
Planning and Development:
- Feasibility Studies: Detailed feasibility studies are conducted to assess the economic viability of the mining project. This includes evaluating the cost of extraction, processing, transportation, and environmental impact.
- Permitting and Approvals: Obtaining the necessary permits and approvals from government authorities is essential before any mining activity can commence. This includes environmental clearances, land acquisition, and community consultations.
-
Mining Operations:
- Open-Pit Mining: Most iron ore is extracted through open-pit mining, which involves removing large quantities of overburden (soil and rock) to access the ore beneath. This method is used when the ore deposits are relatively close to the surface.
- Underground Mining: In cases where the ore deposits are deep underground, underground mining methods such as room-and-pillar or block caving are used. This involves creating tunnels and shafts to reach the ore.
-
Blasting and Excavation:
- Drilling and Blasting: Holes are drilled into the rock and filled with explosives. Controlled blasting is then carried out to break the rock into manageable pieces.
- Excavation and Hauling: The broken rock is excavated using heavy machinery such as excavators and loaders. It is then transported to the processing plant using haul trucks or conveyor belts.
-
Crushing and Screening:
- Primary Crushing: The extracted ore is first crushed into smaller pieces using primary crushers such as jaw crushers or gyratory crushers.
- Secondary Crushing and Screening: The crushed ore is further reduced in size using secondary crushers and screened to separate the ore from the waste material.
-
Beneficiation:
- Grinding: The ore is ground into a fine powder to liberate the iron particles from the surrounding rock.
- Magnetic Separation: Magnetic separators are used to separate the iron ore from the non-magnetic waste material.
- Flotation: In some cases, flotation methods are used to further concentrate the iron ore by separating it from impurities.
-
Pelletizing and Sintering:
- Pelletizing: The concentrated iron ore is mixed with a binder and rolled into small pellets. These pellets are then heated in a furnace to harden them.
- Sintering: Alternatively, the iron ore fines can be sintered to create larger, porous lumps that are suitable for use in blast furnaces.
-
Transportation:
- Rail and Shipping: The processed iron ore is transported to steel mills or export terminals using railways or ships. This requires efficient logistics and infrastructure to handle large volumes of ore.
-
Environmental Management:
- Rehabilitation: After the mining operations are completed, the site is rehabilitated to restore the land to its natural state. This includes re-vegetation, soil stabilization, and water management.
- Waste Management: Proper disposal and management of waste materials such as tailings and overburden are essential to minimize environmental impact.
-
Health and Safety:
- Safety Protocols: Ensuring the safety of workers is paramount in mining operations. This involves implementing strict safety protocols, providing protective equipment, and conducting regular training and drills.
Each of these stages involves complex processes and requires careful planning and execution to ensure the efficient and sustainable extraction of iron ore.
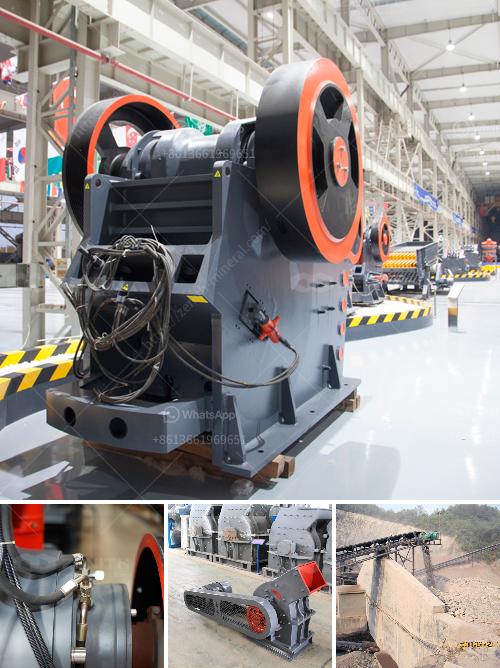